Burnt magnesite brick refers to alkaline refractory products (basic refractory materials), which are fired with periclase as the main raw material. The load softening temperature of Burnt Magnesite Brick is high, and the corrosion resistance of alkaline slag is strong, but the shock resistance is poor, and the corrosion resistance of acid slag is weak. Burnt Magnesite Bricks are mainly used for steelmaking basic open hearth furnaces, furnace walls and furnace bottoms of electric furnaces, permanent linings of oxygen converters, iron mixing furnaces, non-ferrous smelting furnaces, and high-temperature tunnel kilns. The inner lining of the rotary kiln for calcining magnesia and cement, the upper lattice brick of the glass melting furnace, and the bottom and furnace end of the soaking furnace and heating furnace for steel rolling.
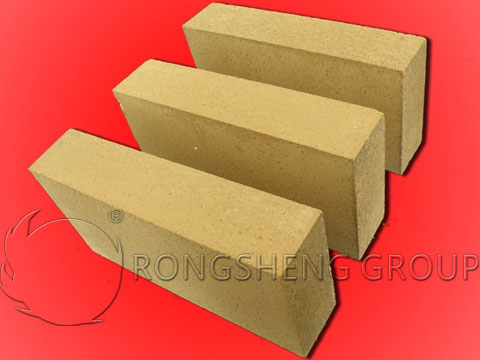
Physical and Chemical Properties of Burnt Magnesite Bricks
Items | Ordinary Magnesia Bricks | High Purity Magnesia Bricks | |
Apparent Porosity / % | 13.5 | 15.0 | |
Load Softening Start Temperature / ℃ | 1550 | ≥1750 | |
Compressive Strength at Room Temperature / MPa | 102 | 92 | |
Chemical Composition / % | SiO2 | 2.85 | 1.50 |
Al2O3 | 1.16 | 0.54 | |
Fe2O3 | 1.97 | 0.85 | |
CaO | 1.61 | 1.20 | |
MgO | 92.0 | 95.51 |
The Manufacturing Process of Burnt Magnesite Brick
1. The optimal particle ratio range of Burnt Magnesite Bricks
Production practice shows that expanding the critical particle size of sintered magnesia from 2mm to 3mm will improve the molding properties of the material and the thermal shock stability of the product. Therefore, the particle part in the particle composition, that is, the 30.5mm part, is controlled at 30~50%, and it is appropriate to be close to 50%. Among them, the particle size is 32mm, and it is appropriate to control it at 18~20%.
The fine powder part in the ingredients, that is, the part <0.088mm, is generally controlled at 35~42%.
The intermediate particles in the ingredients can improve the normal temperature strength and high-temperature strength of the product, and reduce the porosity. The intermediate particles are generally controlled at about 10%.
The particle composition of the ingredients should be determined according to the specific production conditions, the sintering degree of the raw materials, the molding pressure, the sintering temperature, and other process parameters. The sintering degree is good, the molding pressure is large, the firing temperature is high, and the fluctuation range of the particle ratio at all levels can be appropriately relaxed. In addition, an appropriate amount of waste bricks or fired waste products of the same variety can be added to the ingredients.
2. Preparation of mud for sintered magnesia bricks
The sintered magnesia crushed to meet the particle size requirements is placed in the wet mill according to the proportion of ingredients, and the waste liquid of sulfite pulp with a density of 1.2~1.22 g/cm3 is added as a binder, and the addition amount is 34%. Then add magnesia fine powder and mix for 15~30min. Generally, the moisture content of mud is controlled at 23%. Sometimes MgCl2 can also be used as a binding agent. When MgCl2 is used as a binder, the green body has high strength after drying.
If the CaO content in the raw material is high, it must be trapped. The trapping temperature is 10~20℃, and the trapping time is 3~4d.
3. Formed magnesia brick
Forming magnesia bricks should be carried out under high pressure. Usually, a friction brick press of more than 300t is used for molding, and the bulk density of the brick is controlled at 2.90~3.00g/cm3. It can also be formed by a hydraulic press.
Forming operation points. Put the mud material into the model, spread the material evenly, flatten the four corners, and start to pressurize. First light and then heavy, the number of pressures varies depending on the size and shape of the brick, generally 3 to 12 times. In production, the unit weight and external dimensions of the brick are usually controlled to control the bulk density of the brick.
4. Drying and firing of Burnt Magnesite Brick
The drying temperature of magnesia brick blanks should not be too high, generally below 120 °C. Drying is usually carried out in tunnel dryers. The inlet temperature of hot air is 100~150℃, the outlet temperature is 60~90℃, and the residual moisture is controlled at 1.5~0.6%.
Firing should be carried out in a weakly oxidizing atmosphere. In the low-temperature stage, the removal of structural water is accompanied by the volume effect, which can cause cracks in the green body, so the heating rate should not be too fast. After 1300 ℃, the liquid phase begins to appear, the strength increases, and the heating rate can be accelerated. When approaching the firing temperature (1550~1600℃), the number of liquid phases increases, the strength decreases, and the heating rate should be slowed down.
During the cooling process, the temperature can be rapidly lowered before the green body is solidified. After solidification, the “plasticity” of the green body disappears. In order to avoid cracks, the cooling rate should be properly controlled. It can quickly cool down below 800°C.
Matters needing attention in the burning of magnesia bricks
The manufacturing process of Burnt Magnesite Brick is basically the same as that of other refractory bricks, but the following points should be noted.
- (1) The magnesia brick is a barren material, and the moisture content of the mud is low, generally only 2%-3%. In order to increase the plasticity of bricks and the strength of bricks, binders such as sulfite pulp waste liquid or brine are usually added during batching.
- (2) Magnesia bricks have low plasticity. The molding pressure is generally above 80MPa.
- (3) The firing temperature of magnesia brick mainly depends on its chemical mineral composition, which is generally 1550-1600 °C. High-purity magnesia products are 1750°C or higher.
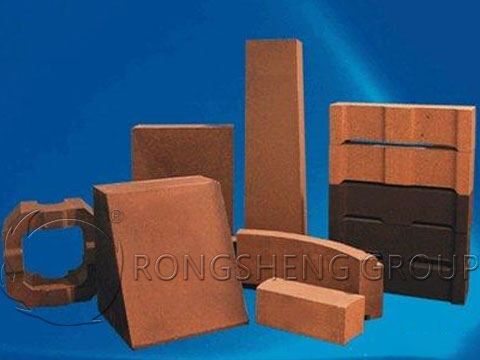
Application of Burnt Magnesite Bricks
Burnt Magnesite Bricks are mainly used for steelmaking basic open hearth furnaces, furnace walls and furnace bottoms of electric furnaces, permanent linings of oxygen converters, iron mixing furnaces, non-ferrous smelting furnaces, and high-temperature tunnel kilns. The inner lining of the rotary kiln for calcining magnesia and cement, the upper lattice brick of the glass melting furnace, and the bottom and furnace end of the soaking furnace and heating furnace for steel rolling.
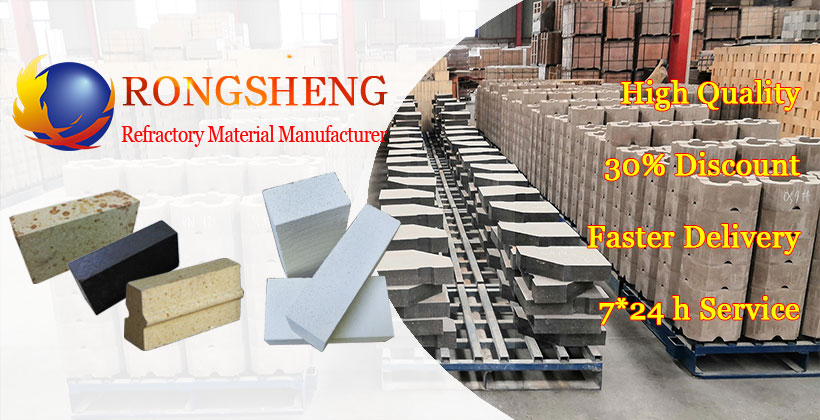
Burnt Magnesia Bricks Manufacturer
Rongsheng refractory brick manufacturer is an experienced refractory brick production and sales manufacturer. Has an independent refractory brick production line. Our refractory products have been sold to more than 70 countries around the world. For Example, South Africa, Philippines, Chile, Malaysia, Indonesia, Vietnam, Kuwait, Turkey, Zambia, Peru, Mexico, Qatar, Egypt, Russia, Kazakhstan, etc. If you need to buy high-quality Burnt Magnesite Bricks, magnesia bricks, and other high-quality refractory bricks, please contact us. We can provide free samples and quotations.