Magnesium Chromium Refractory Bricks for Outokumpu Flash Smelting Furnace
As environmental protection becomes increasingly stringent, the copper metallurgical industry is facing severe challenges. Today, there are two main copper metallurgical methods: the fire method and the wet method. Among them, the fire method plays a major role, and the lining is mainly made of alkaline refractory bricks.
There are many types of pyrometallurgical furnaces. At present, the main pyrometallurgical copper smelting equipment in the world includes flash furnaces, reverberatory furnaces, blast furnaces, Noranda furnaces, and ISA furnaces (Osmet furnaces). There are more than ten kinds of smelting equipment such as Vanukov furnaces, Mitsubishi furnaces, Tenient furnaces, electric furnaces, silver furnaces, and so on. Most processes have problems such as low production capacity, high cost, high energy consumption, and serious pollution. Seriously restricting the development of the copper metallurgical industry.
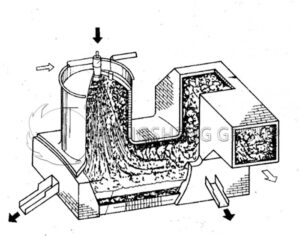
Legend: Outokumpu flash smelting furnace
Outokumpu Flash Smelting Furnace
Since the advent of Outokumpu in Finland in 1949, flash smelting has gradually replaced the reverberatory furnace and blast furnace through continuous improvement, improvement, and development. Today it has become a competitive smelting technology used in today’s copper metallurgy and is generally considered the standard clean copper smelting process.
Currently, more than 50% of global blister copper production is produced using this technology. Due to the mature flash smelting process, it has a high degree of automation, large production capacity, low energy consumption, and good environmental protection. At present, most of the newly built or renovated and expanded copper smelting enterprises in the world adopt the flash smelting process.
Flash Furnace Structure
Outokumpu flash smelting uses oxygen-rich air or hot air at 723~1273K as the oxidizing gas. A down-spray concentrate nozzle is installed at the top of the reaction tower. The dry concentrate and flux are sprayed into the reaction tower at high speed with oxygen-rich air or hot air and are suspended in the tower. During the downward movement of the material, an oxidation reaction occurs with the oxygen in the airflow, releasing a large amount of heat. The temperature in the reaction tower is maintained above 1673K. The material reacts rapidly (2~3s) at high temperatures, and the resulting melt settles into the sedimentation tank. Complete the matte-making and slag-making reactions, and carry out clarification and separation.
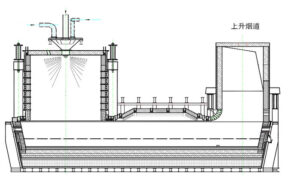
Refractory Materials for Outokumpu Flash Smelting Furnace
Outokumpu flash smelting furnace consists of a reaction tower, sedimentation tank, and rising flue. The operating temperature in the tower is 1400~1500℃. Its work is subject to high temperatures, chemical erosion, and charge erosion, and is easily damaged. Generally, alkaline refractory bricks are used.
The top of the tower is suspended and built with fired magnesia-chromium hanging bricks, with a thickness of about 400mm. The lining around the spray nozzle and burner can be integrally rammed with magnesia-chromium refractory ramming material with a Cr2O3 content of 20%. First, install the finned cooling water pipe on the furnace shell. Lay a 20mm thick insulation board or refractory fiber felt, and then pound the magnesia-chromium refractory ramming material layer. Finally, the working layer is built with cast magnesia chromium bricks. The working layer of the tower wall 1m close to the top of the tower is allowed to be built with fired magnesia chrome bricks. The materials and structure used on the top of the sedimentation tank are the same as those on the top of the tower.
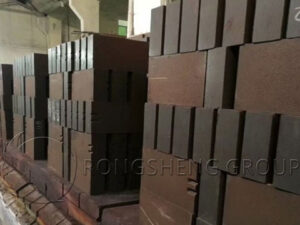
Water-cooled copper sleeves are installed in the slag line area of the pool wall to protect the lining body and are all built with fused magnesia-chromium bricks, while the remaining pool walls are built with fired magnesia-chromium bricks. The total thickness of the anti-arch furnace bottom of the sedimentation tank is about 1800mm. First, 20mm thick asbestos boards or insulation boards are laid against the furnace shell, and 3 layers of clay insulation bricks and 1 layer of clay bricks are laid vertically. Then pound a layer of magnesia-chromium refractory ramming material about 100mm thick. Then use fired magnesia-chromium refractory bricks to build the working layer. The rising flue is on the other side of the sedimentation tank and consists of side walls, sloping end walls, sloping tops, and flat tops. It is mainly built with ordinary fired magnesia chromium bricks.
The lining at the lower part of the inclined end wall is easily corroded, and water-cooled copper sleeves need to be buried to increase the service life. The lining body where the sedimentation tank vault meets the reaction tower and rising flue. Steel beams are used to bear the load and water-cooled copper sleeves with fins are installed, and the working layer is integrally poured with magnesia-chromium refractory castables. Its service life is much longer than that of bricks.
Under normal operating conditions, the service life of the refractory brick lining of a flash smelting furnace is generally 3 to 10 years. During this period, 1 to 3 medium and minor repairs are required.