Is High Alumina Refractory Mortar the Same as High Alumina Cement?
High alumina refractory mortar is prepared from high alumina bauxite clinker, binding agent, and admixture. It is usually delivered in bulk and dry, with water added for reconciliation.
The role of high alumina refractory mortar additives
Soft clay is added to high alumina refractory mortar to improve work abilities, such as spreadability and adhesion. Using soot silica powder instead of soft clay can lower the sintering temperature. Additives mainly include precipitation agents, stabilizers, plasticizers, and anti-shrinking agents. The role of the precipitation agent is to reduce the amount of water added. The stabilizer prevents the solid-liquid separation phenomenon of the adjusted refractory mud during the standing process. Adding plasticizers improves the spreadability of the mud and prevents flow. The anti-shrinking agent is to prevent cracks or peeling caused by volume shrinkage after sintering.
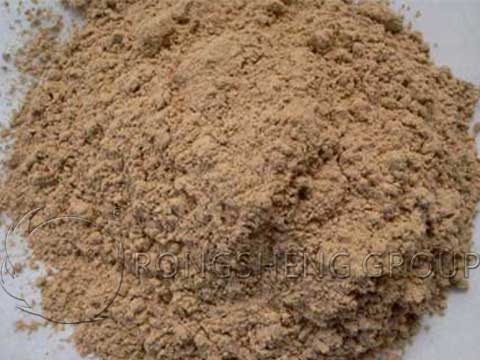
Advantages of high alumina refractory mortar
- (1) Good plasticity and convenient construction.
- (2) High bonding strength and strong corrosion resistance.
- (3) High refractoriness, up to 1750℃.
- (4) Good resistance to slag invasion.
- (5) Good heat peeling.
Use of high alumina refractory mortar
The high-alumina refractory mortar is correctly configured according to the materials of the bricks. Usually, it is mainly used for laying high alumina bricks and corundum bricks.

How to use high alumina refractory mortar
When selecting fire mortar, the chemical composition similar to that of refractory bricks should be considered, so that the thermal expansion of the mud is consistent with the thermal expansion of the bonded refractory bricks to ensure that the masonry can be reliably bonded. It should have good masonry performance and high-temperature performance to bond the refractory bricks into a dense overall furnace lining.
The masonry performance of mortar refers to the work performance of refractory mortar in the masonry process, which is beneficial to ensure the quality of masonry. If there are good fluidity and plasticity. It has certain water retention performance and can maintain a uniform state without segregation and precipitation. It has proper consistency and viscosity during masonry and does not dry up during the brick kneading time, so as to achieve the required thickness of the brick joints, and the mortar in the brick joints is full.
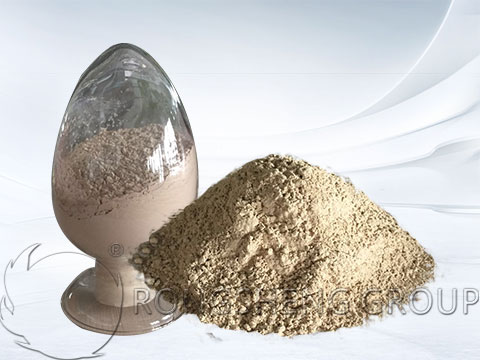
Is high alumina refractory clay the same as high alumina cement?
High alumina refractory clay is different from high alumina cement. Although both high-alumina refractory clay and high-alumina cement are powdered materials, there is a big difference between high-alumina refractory clay and high-alumina cement. High-aluminum refractory mortar is a synthetic material made by processing high-aluminum particles into powders smaller than 180 mesh and adding some binders and coagulants. The high alumina cement is the finished material after calcining bauxite and lime.
High-alumina refractory clay is a refractory material used in the joints of refractory bricks. The powder is high alumina powder plus a certain proportion of binding agent and coagulant. After adding water or adding a liquid binder, stir it into a slurry and apply it to the surface of the refractory brick to adjust the size deviation. It can make the refractory bricks form a tight whole to prevent the damage of high temperature and external force. That is to say, it is the fire clay for bricklaying, which is a kind of finished solid powder.
High alumina cement is a kind of binder in refractory applications, and high alumina cement is also called aluminate cement. It is a clinker with 50% alumina content calcined with bauxite and lime. Aluminate cement is yellow or brown, and high-grade alumina cement is white. The labels are 625#, 725#, 925#, and CA70, CA80.
High-alumina cement is closely related to refractory materials and can be used as a binder for various castables. In addition, some 525# and 425# cement are equipped with gypsum bauxite for construction and special projects. High-alumina cement has a good coagulation effect in the castable, which will make the castable have high-temperature resistance and good strength. It is a raw material for refractory materials.
The high-alumina refractory mortar is also divided into multiple grades, which can be used in conjunction with the construction of refractory bricks of various materials. It is divided into the high-aluminum refractory mortar, phosphoric acid combined with high-aluminum refractory mortar.
Therefore, high-alumina cement and high-alumina refractory mortar are completely different products, but they are closely related to refractory materials. They are also two of the most widely used materials in refractory products.
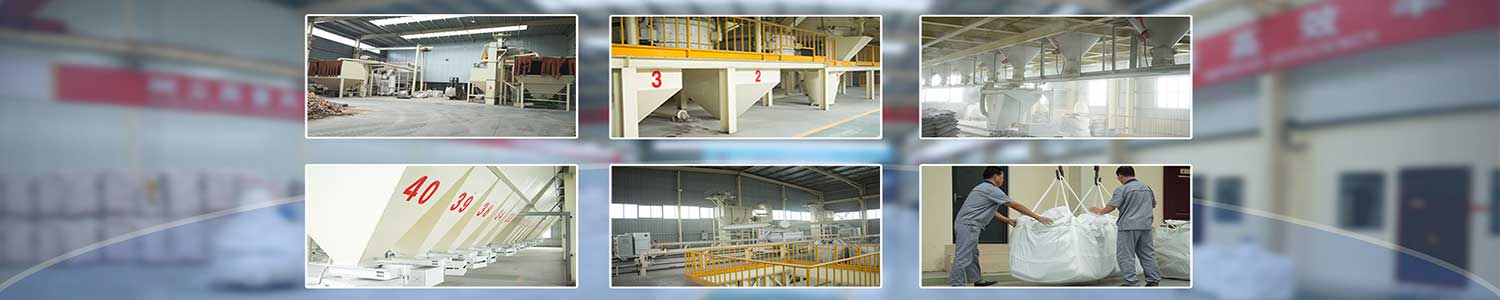
Rongsheng unshaped refractory manufacturer
Rongsheng is a refractory sales manufacturer with an advanced and fully automatic unshaped refractory production line. Rongsheng’s refractory materials have been sold to more than 60 countries around the world. For example, Russia, South Africa, Kazakhstan, Philippines, Chile, Malaysia, Uzbekistan, Indonesia, Vietnam, Kuwait, Turkey, Zambia, Peru, Mexico, Qatar, etc. And got the customer’s continuous return orders. Rongsheng’s unshaped material production line has an annual output of 80,000 tons. Not only can we customize refractory materials according to your specific furnace conditions and production conditions. And can provide you with a refractory solution for the overall kiln lining. If you need to buy unshaped refractory materials, such as high alumina refractory mortar, high alumina refractory castable, high alumina cement, etc. Please contact us. We will provide you with services according to your specific needs.