Spraying Construction Method of Rongsheng High Temperature Refractory Coatings
Refractory spray paint is used to spray new linings and can also be used to repair furnace pipes. Spraying construction method of Rongsheng high-temp refractory coating. It is an effective unshaped refractory material that is easy to construct, extends the service life of the kiln, and reduces the consumption of refractory materials. The material composition of refractory spray paint is basically similar to that of refractory castables of the same type. The difference is that the critical particle size of refractory aggregate is smaller, generally 3~5mm, and is constructed using spraying methods. The dosage of refractory powder, ultrafine powder, and binder is relatively large, generally 35~45%.
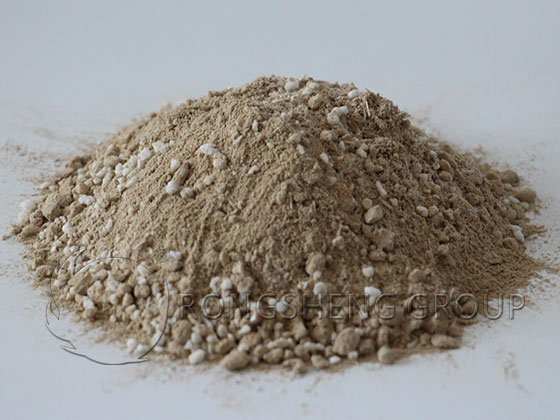
Spraying Process of Refractory Coating
Spraying is carried out using a spray machine or spray gun. The material obtains considerable speed with the help of compressed air and is sprayed onto the sprayed surface through the nozzle, forming a strong spray layer. The key technologies of refractory spray coatings are mainly adhesion, bonding, strength, and sintering. This is also the basic characteristic that the material should have, otherwise the service life of the spray coating will be reduced. These characteristics are not only related to the quality of the material itself, but also affected by the spraying equipment, construction technology, and the state of the sprayed body.
The particles of refractory spray paint cannot be larger than 5mm. Because when it is larger than 5mm, the spray gun will be blocked and normal construction will not be possible. During construction, the refractory spray coating is sprayed 40-50mm into the pipe, and the spray coating can be quickly formed. Generally speaking, the rebound rate of refractory spray coatings produced by refractory spray coating manufacturers is 10%.
In refractory spray coatings, medium and fine particles can greatly improve the adhesion rate, but will increase peeling during drying. Coarse particles can make the repair layer more stable, but too many coarse particles will lead to a high rebound rate and increase the amount of material used. Therefore, the particle gradation must be reasonable and cannot exceed 5mm. Because it exceeds 5mm, the spray gun cannot spray. Reasonable gradation can best improve the construction and use performance of spray coatings.
High-Temperature Refractory Coatings
Refractory spray coatings are divided into light spray coatings and heavy spray coatings. The materials selected according to different use environments include corundum, high alumina, mullite, clay, SiC, magnesium, etc. Mainly used in hot blast furnaces, heating furnaces soaking furnaces, blast furnaces, flues and chimneys, etc. However, lightweight refractory spray coatings are relatively more expensive than heavy refractory spray coatings.
The density of heavy refractory spray paint is generally 1.6-1.8g/cm3. However, there are different requirements in different furnace pipelines. Especially the sintering machine pipes must be made much better than other parts. In other words, this part needs to use refractory spray paint with a density of 2.2g/cm3. Of course, the price of refractory spray paint for sintering machines will be much higher than that of refractory spray paint for other parts.
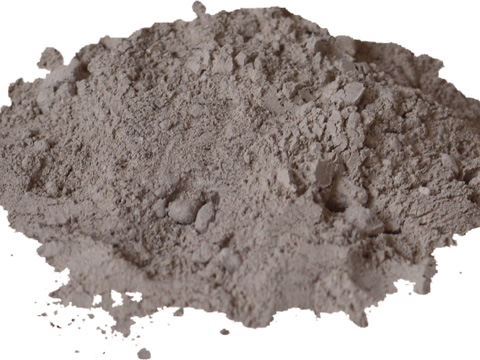
What is Refractory Coating?
(1) Heavy refractory spray paint
The bulk density of heavy refractory spray coatings is generally greater than 1.8g/cm3. Refractory aggregates and powders generally use aluminum silicate materials, with a critical particle size of 5 or 10 mm. Particle composition: 3~5mm is about 30%, 1~3mm is about 30%. Less than 1mm is about 40%. The binding agent is aluminate cement and water glass, plus additives. Generally, semi-dry method or false dry method is used for construction.
Main properties of heavy refractory castables. The medium temperature strength of CA-50 cement spray coating is reduced. However, water glass and phosphate spray coatings increase with the increase of heating temperature, and their bulk density is slightly lower than the same type of refractory castables produced by vibration molding.
In recent years, medium-heavy refractory spray coatings with a bulk density of 1.8~2.1g/cm3 have been developed. That is, on the basis of heavy materials, 3% to 6% expanded perlite or 5% to 20% porous light clinker is added. It is mainly used on the heat insulation layer of kilns and has good heat preservation effect.
(2)Lightweight refractory spray coating
There are many varieties of lightweight refractory spray coatings, mainly including clay, ceramsite, perlite and other refractory spray coatings. Lightweight refractory spray paint is mainly used for the thermal insulation layer of kilns, and can also be used for the working layer of tubular heating furnaces, flues and chimneys.
The critical particle size of refractory aggregate for lightweight refractory spray paint is 5mm. The particle gradation is: 3~5mm, about 19%~30%. 0.6~3mm is about 8%~14%. 0.088~0.60mm is about 30%~40%, and less than 0.088mm is about 25%~35%.
The main properties of lightweight refractory spray coatings. During the spraying construction process of refractory spray paint, the original particle gradation will be greatly changed due to the rebound and scattering of refractory aggregates and the splashing of refractory powder. Therefore, when the aggregate size requirements of the refractory spray coating are certain, in order to make the aggregate gradation of the actual spray coating meet the requirements, the original gradation before spraying must be adjusted to meet the requirements after spraying.
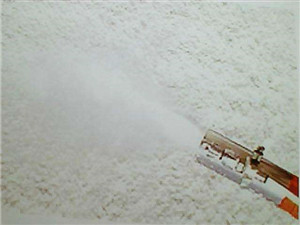
Spraying construction of Rongsheng Refractory Spray Coating
Before spraying paint, test spraying should be carried out in accordance with the construction instructions provided by the manufacturer for the brand of spray paint. To determine the appropriate parameters, such as wind pressure, water pressure, etc.
Several commonly used spray coatings
- (1) When spraying clay materials at room temperature, the aggregate particle size should be below 3.5mm. When the spray paint lacks viscosity, 2% clay should be added to improve its construction performance.
- (2) When spraying high-aluminum materials at room temperature, additives should be added to prevent falling and increase the density of reinforced metal parts.
- (3) When lightweight insulation materials are used for spraying, lightweight aggregates with higher strength should be used, and appropriate amounts of asbestos and clay should be added. Aggregates with low strength, brittle under pressure and friction, or elastic aggregates are not suitable for spraying. The volume density of lightweight thermal insulation spray paint should be between 0.7~1.3t/m3.
Reinforcement metal parts
Spraying construction must be reinforced with metal supports. Metal supports should have the characteristics of simple shape, small size, and reliable performance. Generally, it should be made of round steel.
When the thickness of the spray coating is 35~75mm, metal mesh should be used for reinforcement. The diameter of the metal mesh is Φ3.2~4.2mm, and the mesh size should be 1.5 times the thickness of the spray coating. And it is fixed on the furnace wall by welding, binding, and crimping.
When the spray thickness is more than 100mm, round steel of 4~8mm should be used to make V-shaped or Y-shaped metal parts and welded to the furnace shell.
The installation distance of metal parts: the side wall part should be 3 times the thickness of the spray coating, and the top part should be 1.5~1.8 times the thickness of the spray coating. The distance from the front end of the metal anchor to the surface of the spray coating should be 50mm for the side wall and 25~30mm for the ceiling.
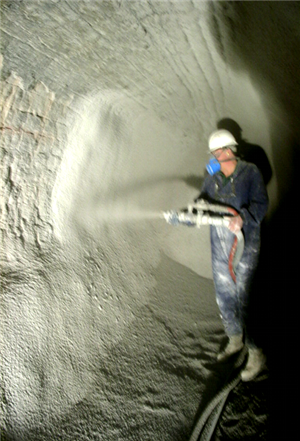
Process inspection before spraying
The following process inspections should be carried out before spraying refractory spray paint:
- (1) Before spraying, the installation position, spacing size, and welding quality of the metal supports should be checked and cleaned.
- (2) When there is a fixed steel wire mesh on the support frame, check whether the anchoring quality of the steel wire mesh meets the requirements. The upper, lower, left, and right sides of the steel wire should overlap one grid. The overlap shall not exceed three layers and the fasteners shall be oriented toward the non-working layer.
- (3) Check the sprayed surface. There should be no floating rust, dust accumulation, oil stains, or water immersion on the sprayed surface.
Spraying operations and adjustments
Refractory spray paint is sprayed onto the sprayed surface with a spray gun. Materials constructed by spraying are called refractory spray paint. Spraying is carried out using spray machines and spray guns. The refractory spray paint uses compressed air or mechanical pressure in the pipeline to obtain sufficient pressure and flow rate. Spray onto the sprayed surface through the nozzle to form a solid spray layer.
The spraying methods of refractory spray coatings are divided into three categories: wet method, dry method, and flame method. When constructing refractory spray coatings, appropriate construction plans for high-temperature coatings and refractory coatings can be specified based on actual working conditions. To extend the service life of the kiln lining.