Corundum Castable that is Resistant to High Temperatures and Slag Erosion
Corundum castable is a high-grade castable in a series of unshaped refractory materials. It has a stable crystal structure has more stable performance in high-temperature sintering processes, and is suitable for use in high-temperature areas lined with various kilns. Corundum castable that is resistant to high temperatures and slag erosion. Refractory castables made of this material can better reflect its fire resistance and wear resistance at high temperatures. Its thermal shock resistance can also achieve better performance at high temperatures, and its performance is reliable and reliable during high-temperature operation of the kiln.
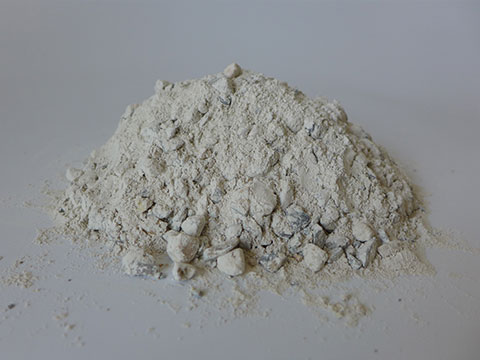
High-Grade Corundum Castable
Corundum castable is used in high-temperature parts of industrial kilns between 1400℃ and 1650℃. It is produced using bauxite clinker and corundum with an aluminum content of more than 90% as aggregate, using micro-powder technology and pure calcium aluminate cement. This kind of corundum refractory castable has high strength, high volume density, and strong high-temperature stability. Used in high-temperature parts of industrial kiln linings, it has strong resistance to slag erosion, wear resistance, and high-temperature gas erosion resistance.
Performance Characteristics of Corundum Castables
Corundum castables have high-energy effects of high temperature resistance and corrosion resistance, and can still maintain stable performance under long-term use. It can be combined with silicon carbide, mullite, andalusite, sillimanite, etc. to make composite refractory castables. It can be used in high-temperature furnace lining parts in different atmospheres.
The high-temperature main crystal phase of corundum castable is corundum refractory castable. It is a refractory castable prepared with special high-alumina bauxite clinker or fused brown corundum as aggregate, adding refractory powder, pure calcium aluminate cement binder, silica powder, and admixtures. Usually, the pouring method is used for construction. It can be cast into a complete lining, or prefabricated blocks of castable materials customized by the manufacturer can be spliced on-site for use.

Product Features of Corundum Castables
- (1) High compressive strength and strong lining stability at high temperatures.
- (2) The volume density is high, and the overall lining has strong resistance to slag erosion and permeability.
- (3) Strong resistance to erosion by solid particles, dust, and high-temperature gases.
- (4) Low mechanical wear resistance.
- (5) Not affected by reducing gases such as H2 and CO.
Corundum Castable Product Uses
The use temperature of corundum castable is 1600-1700℃, and it is mainly used as lining material for various high-temperature kilns and high-temperature structures. Such as the outer lining of the impregnation tube of the molten steel vacuum degassing device, the lining of the spray metallurgy, and the argon-blowing integral spray gun. The lining body of the electric furnace top triangular area and the LF furnace cover. High-temperature wear-resistant lining for catalytic cracking reactors in the petrochemical industry. High-temperature wear-resistant lining for circulating fluidized beds and power plant boilers.
How to Improve the High-Temperature Slag Corrosion Resistance of Corundum Castables?
The development trend of dense refractory castables requires the calcium aluminate cement content to be reduced as much as possible while maintaining good green strength and high-temperature mechanical properties. The key technology is to increase the packing density between particles. The above purpose can be effectively achieved by adding micron powder, submicron powder, or even nano-alumina powder. The reasons are:
- 1) Reduce the CaO content in the castable and reduce the low melting phase generated at high temperatures. It can significantly improve the high-temperature mechanical properties of castables.
- 2) Promote sintering at medium temperature and increase the medium temperature strength of castables.
- 3) Reduce the total amount of water added and increase the density of the castable.
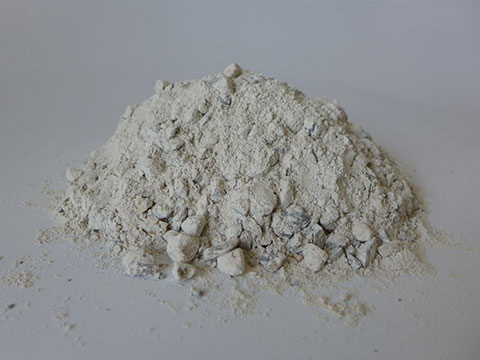
In terms of comprehensive cost performance, the role of alumina micropowder cannot be ignored. Its particle morphology, size, particle size distribution and specific surface area will have a great impact on the performance of the castable. In particular, the particle size distribution plays an important role in filling the pores between aggregates and increasing the packing density. Research has found that using composite micropowders with different particle size distributions can significantly increase the packing density. Reducing water consumption is beneficial to mechanical properties such as high-temperature flexural resistance and post-thermal shock strength. Li Wenping studied the influence of alumina powder particle size on the properties of castables. It was found that as the particle size of the micropowder decreases, the flowability and setting time of the castables both show an increasing trend.
More importantly, alumina micro-powder can promote the formation reaction of the CA6 phase of calcium aluminate cement at high temperatures, thereby significantly improving the high-temperature properties of castables. Pinto et al. found that the particle size of alumina powder decreased. It can nearly double the flexural strength of castables containing 1% (mass fraction) CAC cement and promote the formation of the CA6 phase. Auvray et al. discovered the optimization of alumina micro-powder and the in-situ generation of CA6. Ceramic bonding can be formed in the castable, which significantly improves the high-temperature elastic modulus of the castable. Specifically,
- 1) As the alumina fine powder content increases and the corundum fine powder content decreases, the normal temperature performance and high-temperature performance of the castable samples after heat treatment at different temperatures are improved to varying degrees. After being treated at 1600°C, the normal temperature flexural strength, normal temperature elastic modulus, and elastic modulus at 1400°C can be increased by 53.9%, 47.9%, and 40.4% respectively.
- 2) Adding too much micro powder is detrimental to the thermal shock stability of the castable. The more the amount of alumina powder is added, the residual flexural strength retention rate of the sample after thermal shock decreases with the increase in the amount of alumina powder. After three water-cooling thermal shocks, the residual flexural strength retention rate of the material decreased from 18.45% to 11.97%.
- 3) As the content of aluminum oxide powder increases, the slag erosion resistance of the castable gradually increases, and the thickness of the permeable layer decreases from 2.9mm to 2.1mm. The higher content of micro-powder will make the pore diameter of the castable smaller, promote the interpenetration and bonding of plate-like CA6 in the original layer, and make the matrix bonding closer. It is beneficial to improve the slag resistance performance of castables.
To purchase high-quality corundum castable refractory lining materials, please contact us.