Cordierite Bricks for Hot Stove Burners
The hot blast stove burner is a device that mixes gas and air and sends them into combustion. The burner used in the hot blast stove is divided into two types: metal material and ceramic material. Among them, the ceramic burner is mainly made of mullite or cordierite-mullite refractory materials. The lining refractory material of the hot blast stove and its construction quality will directly affect the thermal insulation effect of the furnace body and the stability of the furnace lining structure, thus having a profound impact on the life of the furnace body and design efficiency.
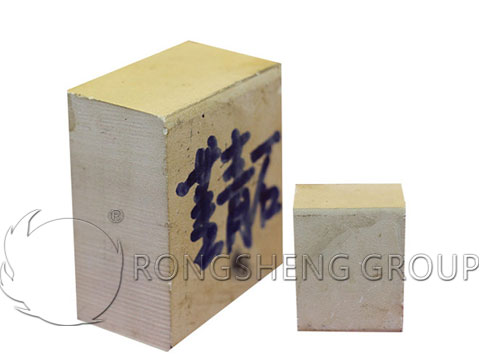
Brief Introduction of Cordierite Mullite Bricks
Friends who have not been in contact with cordierite mullite bricks will be very unfamiliar with this refractory brick. Today, Rongsheng Factory will introduce the product knowledge of cordierite mullite bricks to you, hoping to provide help to friends who need refractory bricks for ceramic burners in hot air stoves.
Cordierite mullite brick is a novel refractory material in the 1980s. It has the characteristics of high refractoriness, good thermal shock resistance, high load softening temperature, small expansion coefficient, and long service life. Cordierite mullite bricks are widely used in the light industrial ceramics industry, tunnel kiln car bricks, raceway kilns, pusher kilns, pusher kiln furniture, saggers of various specifications, etc. It is also suitable for kiln car surfaces in the ceramic industry, porous kiln push plates, roller kiln gaskets, and sagger for ceramics. It replaces clay refractory materials and high alumina refractory materials. It works well.
Cordierite Bricks for Ceramic Burner of Hot Stove
A burner is a device used to mix gas and air and send them into the combustion chamber. It is generally required to have sufficient combustion capacity, which is beneficial to shorten the burning period. It is necessary to ensure that the gas and air are mixed evenly and can be burned stably to avoid back spraying.
In order to improve the combustion capacity and meet the needs of high wind temperatures, ceramic burners are used. The ceramic burner is a burner made of refractory materials and installed in the combustion chamber. Gas and air pass through a special structure before combustion so that the airflow is divided into small streams (called trickle segmentation), mixed with each other after spraying out, and then burned in the room. Obviously, from the function of the ceramic burner, its working environment is subjected to the thermal shock of the sharp temperature change during the heat exchange process. Taking a steel factory as an example, each blast furnace has 4 hot blast stoves for the hot blast. When the hot blast stove is in normal production, it takes 35 minutes to heat up and 45 minutes to supply air. The brick temperature fluctuates from 500-600°C to as high as 1000°C at the moment when the ceramic burner starts to burn after the air is supplied. The thermal shock to refractory bricks is obvious. In addition, it is also impacted by combustion gas, so the corresponding refractory material should have better thermal shock resistance.
If the hot blast stove is an external combustion type. Traditional bricks for ceramic burners are cordierite bricks, but now they have been developed to use andalusite-mullite refractory bricks materials, high alumina cordierite bricks, mullite cordierite bricks, etc.
If it is a top-fired hot blast stove, the air temperature of the ceramic burner is relatively high (about 1360°C). Higher thermal shock resistance is required, which is reflected in the test conditions and the number of thermal shock stability. Originally required 1300°C, water cooling now requires 1100°C, and water cooling, thermal shock stability is not less than 100 times. The production of these bricks also uses three-stone minerals, especially andalusite minerals.
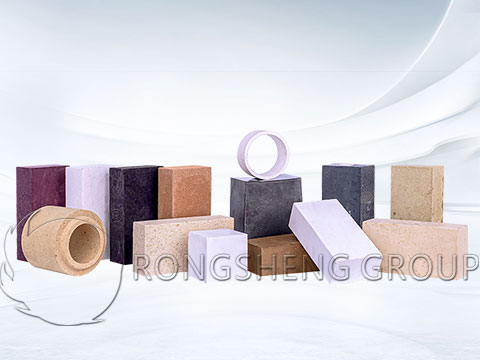
Rongsheng Refractory Brick Manufacturer
The cordierite bricks for hot blast stove burners produced by Rongsheng refractory brick manufacturers have good thermal stability and a small thermal expansion coefficient. Based on the principle of being responsible to customers, Rongsheng manufacturers strictly control the production standards of refractory products. To ensure that the produced refractory cement, refractory bricks, castables, and other products can have good high-temperature resistance and strong slag resistance. It can meet the operating temperature of the customer’s actual boiler. The product quality has been well received and supported by new and old customers. Buy cordierite bricks, cordierite mullite bricks, mullite refractory bricks, factory direct sales, and refractory materials at reasonable prices. Welcome to consult and purchase, Rongsheng refractory products and customer service will not let you down.