The Effect of Cement Addition on the Performance of Ladle Porous Plugs and Well Blocks
Ladle Porous Plugs are the most critical functional element in the bottom argon blowing process for molten steel refining, and their use conditions are very harsh. Ladle Porous Plugs can be divided into two types according to the assembly method: internal integral Porous Plugs and External combination Porous Plugs. The Porous Plugs’ core needs to be protected by supporting brick. At present, the well blocks for ladle are generally casted and used directly after curing, drying, and baking. The well blocks mainly undergo the following effects during use. (1) The brick working face is repeatedly subjected to rapid cooling and heating, which easily causes the brick to break and peel off. (2) Corroded and penetrated by molten steel and slag. (3) It is strongly scoured and worn by high-temperature molten steel. Therefore, it is required that the well blocks for ladle should have high strength, good thermal shock resistance, and excellent slag erosion resistance.
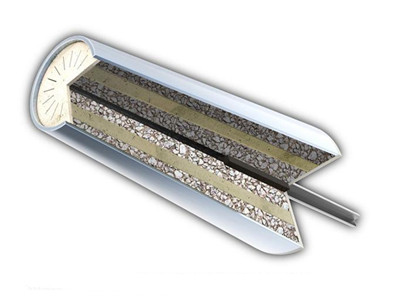
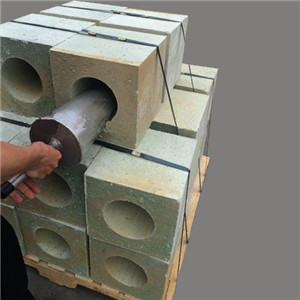
The well blocks for ladle often appear cracks, transverse fractures, and block-dropping phenomena during use. It seriously affects its service life, and improving its thermal shock resistance is an important way to increase its service life. At present, there are many kinds of research on Porous Plugs, but not much researches on well blocks for the ladle. In this work, the effect of cement addition on the performance of corundum spinel ladles Porous Plugs was studied. It is expected to increase the service life of the Porous Plugs block, enhance its safety factor, and meet the requirements of steelmaking plants.
The effect of cement addition on the performance of ladle Porous Plugs and well blocks
- (1) With the increase of cement addition, the normal temperature flexural strength and compressive strength of the sample after drying at 110°C gradually increase. The normal temperature flexural strength and compressive strength of the sample after being burned at 1560°C first increase, then decrease, and then increase. The linear change after burning first increases and then decreases. When the cement content is 6% (w), the strength is lowest. The apparent porosity and linear change rate after firing are the largest, and its performance is the worst.
- (2) With the increase of cement addition, after three thermal shocks after water cooling at 1100°C, the strength retention rate of the sample after firing at 1560°C gradually increases, and the thermal shock resistance is improved. When the mass fraction of cement is 10%, the thermal shock resistance is the best.
- (3) The anti-burst performance of the samples added with an anti-explosion agent is obviously improved. Especially the anti-explosive effect of sodium bicarbonate or sodium bicarbonate + polypropylene organic fiber composite is the best.
- (4) The service life of high-purity corundum spinel bottom-blown argon-blown ventilating bricks with a cement addition amount of 6%-10% (w) and a compound explosion-proof agent has been increased from the original average of 31 times to an average of 36 times.
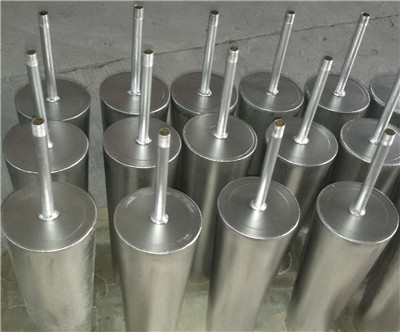
Comparison of performance of chrome corundum Porous Plugs block and corundum-spinel Porous Plugs block
Chrome corundum, as a traditional material for ladle Porous Plugs block, has played a very important role for a long time. Due to the insufficient performance of traditional chrome corundum bricks in thermal shock resistance, it is prone to cracks during use. It is very easy for molten steel to invade the brick body along the gas inlet that produces cracks, forming molten steel penetration, which will seriously affect the effect of argon blowing. In addition, chromium can also pollute the environment. Therefore, chrome corundum Porous Plugs block have been gradually replaced by corundum spinel Porous Plugs block with better performance. However, chromium corundum Porous Plugs blocks are better than corundum-spinel Porous Plugs blocks in terms of body stability and resistance to slag penetration.
Performance Comparison of Chrome Corundum Brick and Corundum-Spinel Brick
The material of chromium corundum is a sintered tabular corundum with compact structure, low porosity, and easy sintering as the main raw material. There are some differences in the performance of the two types of Porous Plugs blocks. Generally speaking, the volume density of the corundum-spinel Porous Plugs block is smaller than that of chrome corundum Porous Plugs block under the same particle size gradation. The porosity of corundum-spinel brick is lower than that of chrome corundum brick. This is because, during the firing process, the swelling of the body caused by the formation of spinel offsets part of the shrinkage caused by the fine powder, resulting in a decrease in porosity. On the other hand, the linear change rate of the corundum-spinel Porous Plugs block is slightly larger than that of the chrome corundum Porous Plugs block. That is to say, the volume stability of corundum-spinel Porous Plugs blocks is not as good as that of chrome corundum bricks, mainly because magnesia alumina spinel is generated during the firing of corundum-spinel Porous Plugs blocks.
Since the slits of slit-type Porous Plugs blocks are relatively narrow, generally about 200 μm. If the volume of the Porous Plugs block changes greatly during the firing process, it will affect the size of the slits, and ultimately affect the air permeability and blowing effect. As a result, the performance of the Porous Plugs block is reduced during the use, the blowing rate is reduced, and even the blowing is blocked. Since the thermal shock stability of the spinel is better than that of corundum, the thermal shock stability of the corundum-spinel Porous Plugs block is better than that of chrome corundum Porous Plugs block. The corrosion index of the two slag resistance is the same, but the slag penetration resistance of the chrome corundum brick is stronger than that of the corundum-spinel brick.
Generally speaking, corundum-spinel Porous Plugs blocks are better than traditional chrome corundum Porous Plugs blocks in terms of performance. The traditional chrome corundum Porous Plugs block has been gradually replaced by it. Corundum-spinel Porous Plugs blocks are gradually becoming the mainstream ladle Porous Plugs blocks today.
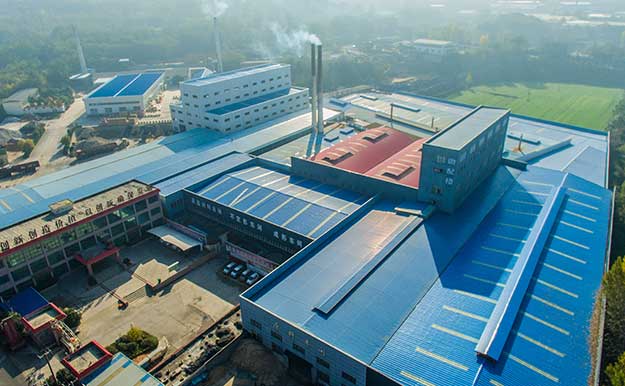
Rongsheng Kiln Refractory Material Manufacturer
Rongsheng is an experienced refractory material manufacturer and sales company. Rongsheng’s refractory products have served refractory lining projects in more than 60 countries around the world. We have a wealth of refractory lining solutions for refractory linings for steel smelting furnaces, glass kilns, and cement kilns. If you want to buy refractory materials for ladle, please contact us. We will provide you with services according to your specific needs.