How to Choose Refractory Lining for Blast Furnace?
How to choose refractory lining for blast furnace? In the design of refractory materials for blast furnaces, the different working conditions and erosion mechanisms of each part of the blast furnace should be fully considered, combined with the conditions of the original fuel, and the refractory materials should be selected in a targeted manner. The high-quality Refractory Lining for Blast Furnace, which can not only improve the service life of the blast furnace but also greatly save the production cost.
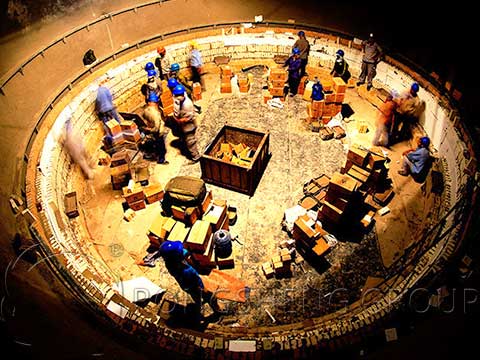
Therefore, according to the different working conditions of different parts of the blast furnace, the selection of refractory lining for blast furnace used in each part is as follows.
(1) Furnace bottom, hearth, taphole area, and tuyere belt.
The development of longevity technology in the hearth and hearth bottom has gone through a long process. The mainstream models of the entire hearth and hearth bottom structure are the “carbon + ceramic composite hearth and hearth bottom” structure and the “carbonaceous hearth + integrated hearth bottom” structure, these two technical systems.
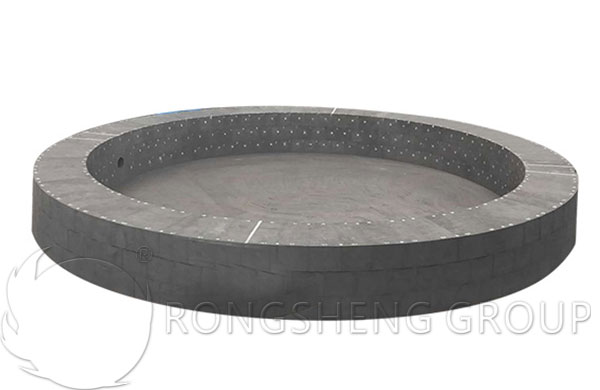
The heat-resistant castable is used below the furnace bottom water-cooling pipe centerline to the elevation of the heat-resistant foundation pier top. Carbon refractory ramming material is used between the centerline of the furnace bottom water-cooled pipe and the first layer of fully covered carbon brick. The first, second, and third layers are covered with semi-graphite carbon blocks, and the fourth layer is covered with microporous carbon bricks. There are also carbon bricks and ultra-microporous carbon bricks, the bottom of the furnace is made of two layers of ceramic pads, and the hearth is made of ceramic walls. The ceramic is beneficial to the heat preservation of the hearth slag and is conducive to saving the coke ratio and active hearth.
By adopting strong cooling measures in which the furnace bottom water cooling tube is buried under the furnace bottom brick, and the building method of the carbon furnace and ceramic. The goal of reducing erosion rate and longevity of blast furnace can be achieved.
The taphole area is built with carbon composite bricks. A composite brown corundum combined brick structure is adopted in the tuyere area. Its anti-slag iron corrosion and thermal shock resistance are good, the overall performance is good, and it has good protection for the tuyere-cooler casings. At the same time, it supports the refractory brick lining of the furnace belly.
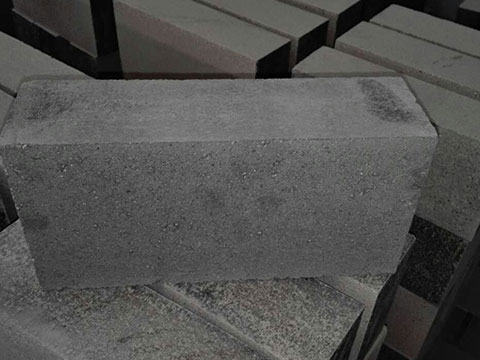
(2) The area of furnace belly, furnace waist, and furnace body.
A thin furnace lining structure with an integrated refractory brick wall is adopted, and the lining of cast iron cooling plate refractory brick is integrated with the cooling wall by cold setting. The production practice of the steel mill proves that this design structure can fully meet the normal service life of the blast furnace for 12-15 years.
The furnace belly, furnace waist, and lower part of the furnace body are inlaid with silicon carbide bricks combined with silicon nitride. The middle of the furnace body is made of fired microporous aluminum carbon brick. The middle and upper parts of the furnace body are lined with phosphoric acid-impregnated high-density clay bricks.
(3) Refractories for furnace throat
Furnace throat plays a role in protecting furnace lining and reasonable cloth. This area is mainly affected by direct impact and friction from blast furnace incoming materials. Because the temperature of this part is not high, about 400~500℃, the refractory materials used are mostly dense clay bricks, high alumina bricks, and sillimanite bricks. But the service life is still short, so it is also protected by wear-resistant and impact-resistant cast steel bricks.
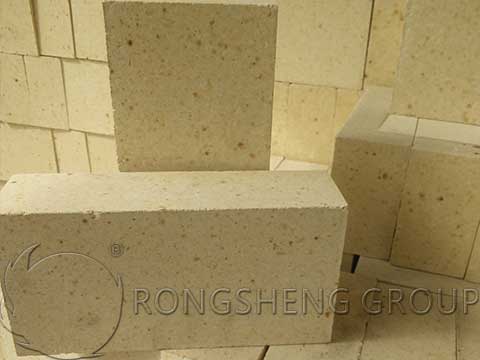
(4) Furnace top and riser.
Spraying materials with strong CO corrosion resistance and high thermal flexural strength.
(5) Between the cooling stave and the furnace shell.
The grout is pressed into the refractory mortar without water.
Rongsheng refractory brick manufacturer
Rongsheng is a refractory manufacturer with more than ten years of production and sales experience. Our refractory brick and refractory castable production lines are equipped with advanced production equipment. Moreover, our experienced technical engineers of refractory materials always pay attention to the development of refractory materials and customize refractory products for customers’ refractory linings. Our refractory products have been sold to more than 60 countries around the world, such as Malaysia, South Africa, India, Indonesia, Pakistan, Netherlands, Kuwait, Kenya, Russia, United States, etc. If your blast furnace needs refractory bricks or refractory castables. Please contact us with your details requirements, we will provide you with efficient refractory service.