Rongsheng Refractory Cement for Sale in Philippines
Refractory Cement for Sale is also called bauxite cement, high alumina cement, aluminate cement. According to the national standard GB201-2000, refractory cement is also collectively referred to as CA50 aluminate cement. In order to distinguish the strength of cement, such symbols are often used to indicate: CA50-A600, CA50-700, CA50-A900, etc. Refractory cement is a fast-setting, fast-hardening, high-strength high-temperature binder. The initial setting time is generally about 2 hours. The final setting time is generally about 4 hours. The strength can reach 70% within three days, and the strength can reach 100% of the overall strength within 28 days. Refractory cement, high alumina fine powder, high alumina aggregate, and other additives are formulated into refractory castables according to a certain particle gradation. Rongsheng Refractory Cement for Sale, Its refractory temperature can reach 1500 degrees Celsius, and it is widely used in high-temperature furnace engineering.
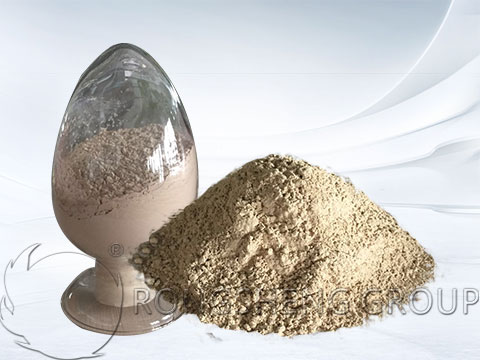
Classification of Refractory Cement for Sale
Refractory cement is one of the main materials for making high-temperature furnace linings. It is Refractory Cement for Sale with refractoriness not lower than 1580°C. According to different compositions, it can be divided into aluminate refractory cement, low calcium aluminate refractory cement, calcium magnesium aluminate cement, and dolomite refractory cement.
Aluminate cement can be divided into four categories according to Al2O3 content:
- CA-50, 50%≤Al2O3<60%
- CA-60, 60%≤Al2O3<68%
- CA-70, 60%≤Al2O3<77%
- CA-80, 77%≤Al2O3
The Main Components of Refractory Cement
Refractory cement refers to cement with calcium aluminate as the main component. Refractory Cement for Sale is the basic bonding agent of unshaped refractory-casting refractory. Its chemical composition is mainly Al2O3 and CaO, and some also contain quite a lot of Fe2O3 and SiO2. The mineral composition consists of the following three kinds of minerals, CaO·Al2O3 (CA), CaO·2Al2O3 (CA2), 12CaO·7Al2O3 (C12A7) three compounds. And it is composed of 2CaO·Al2O3·SiO2 (C2AS) containing inclusions and 4CaO·Al2O3·Fe2O3 (C4AF).
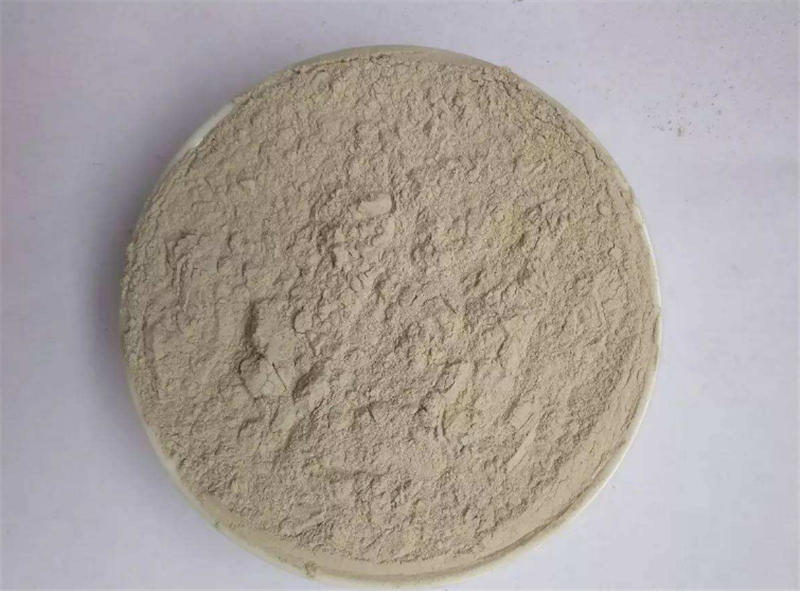
Properties of Refractory Cement
The properties of Refractory Cement for Sale mainly depend on its mineral composition. The main mineral of refractory cement is monocalcium aluminate (CA), which has a high hydraulic activity and coagulates. Although it is not very fast, it hardens quickly, and the hardening time does not exceed one day. It is the main source of the strength of high alumina cement, especially the early strength. Calcium aluminate (CA2) has slower hydration and hardening, with lower early strength and higher late strength. the C12A7 has the characteristics of fast hydration and fast setting, but the strength is not high. In ordinary high alumina cement containing inclusions ( C2AS and C4AF), C4AS plays a role in hardening the cement as soon as possible. In high-grade high-alumina cement, C12A7 plays a hardening role. As for C2AS, basically it does not produce hydration, so it cannot show its strength.
Refractory cement contains 5 kinds of calcium aluminate minerals, and these calcium aluminates will show intense heat generation as the hydration reaction proceeds. Ordinary high-alumina cement contains 53-55% Al2O3. After 5-8 hours, the temperature reaches a peak value of 80-90℃. The high-alumina cement containing 70% Al2O3 will reach the peak temperature after 10-12h and the high-alumina cement containing 80% Al2O3 after 8-10h, which are 80 ℃ and 70 ℃ respectively.
The heating temperature and the time to reach the maximum temperature of a single cast of different types of high alumina cement are determined by the heating characteristics and content of the calcium aluminate contained.
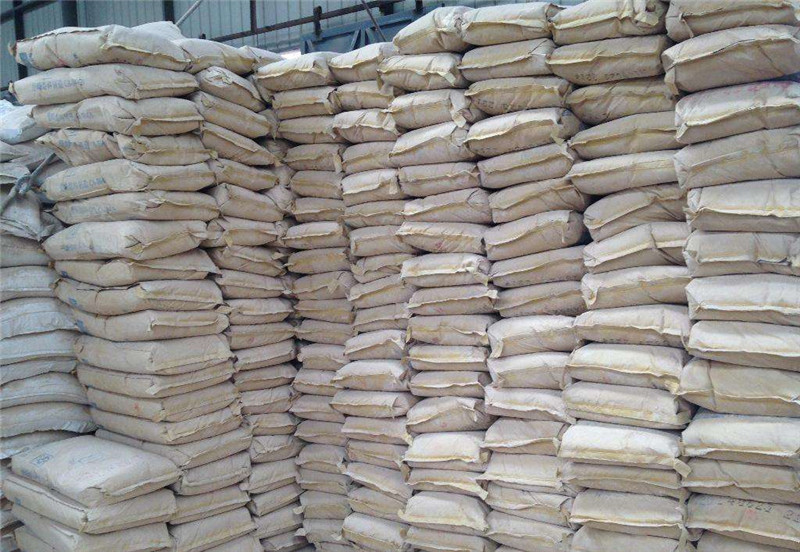
How to Use Refractory Cement
The use of refractory cement is very simple, it can harden after adding water and mixing. Generally, there is no need to add other binders, but some refractory aggregates and powders can be added. If only refractory cement is used, a lot of cracks will occur after high temperature. It can be used to cement various refractory aggregates, such as corundum, calcined high alumina bauxite, etc. It is made into the refractory mortar or refractory castable, which is used as lining of cement rotary kiln and other industrial kilns.
Precautions for Refractory Cement
Many people tend to confuse refractory cement with refractory soil. If refractory cement and refractory soil are used together, the use-value of refractory cement will be greatly reduced. It is equivalent to mixing refractory cement and loess together. The solidification strength and marking of refractory cement will be much lower. It is recommended that workers who have been engaged in furnace construction for a long time, in refractory construction, use refractory cement and refractory soil rigorously.
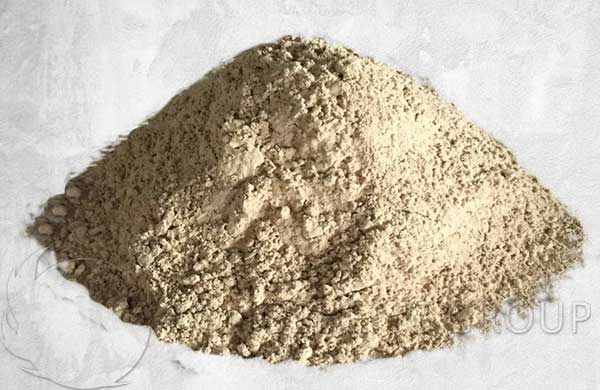
Refractory Cement for Sale Price
Because refractory cement has the following characteristics, the consideration of the Refractory Cement for Sale price also needs to be analyzed according to specific working conditions.
- Refractory cement is a bonding agent used in thermal kilns or wall linings.
- This type of cement is different from other types of cement, it still maintains a firm bond under high-temperature conditions.
- Refractory cement will have a certain strength at room temperature, which is used to ensure the hardened shape of the preform.
- In addition, refractory cement solidified at room temperature has some physical and chemical advantages. For example, through the cement solidification process, the internal moisture of the cement product can be quickly precipitated, or the internal structure can be tightly reinforced.
The price of commonly used refractory cement is generally 1800 yuan per ton. Some users need a small amount of refractory cement to make small furnaces, and the price at this time is calculated according to the price of each bag.
What is the price of refractory cement for boilers? There are also many types of refractory cement for boilers, mainly because of the different aluminum content. The general CA-50 is about 1500, the cheaper one can reach about 1200, and the most expensive CA-80 and 70 can reach 5 to 6 thousand tons. The refractory cement prices listed in this article come from the Internet and are for reference only. The specific price is subject to the price provided by the supplier at the time of purchase. Get more details on refractory cement Philippines for sale. Please leave us your requirements.