In recent years, due to the vigorous development of out-of-furnace refining technology and continuous casting technology, the ladle as a container for holding molten steel and molten steel refining equipment has greatly extended the residence time of molten steel in the ladle. Accompanied by the increase in the tapping temperature and harsher smelting conditions, the service life of the ladle lining is greatly reduced. The ladle adopts Alumina Magnesia Refractory Castables, including spinel-containing castables, for integral casting, which has always been a development trend.
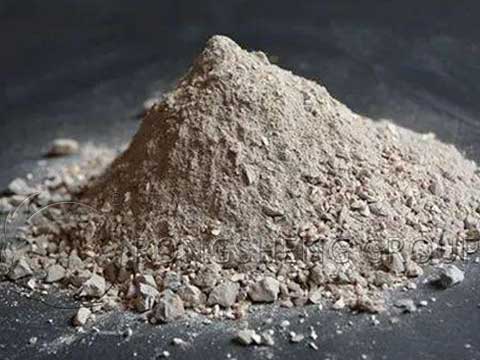
Introduction of Alumina Magnesia Refractory Castables
Alumina Magnesia Refractory Castables are refractory castables with corundum as aggregate, spinel material, and corundum powder as a matrix, and pure calcium aluminate cement as a binder. Its chemical composition is Al2O3 89%~93%, MgO 5%~8%. It has good corrosion resistance and slag penetration resistance and can be used as a large ladle lining for continuous casting.
Alumina-magnesia spinel castable
The alumina-magnesia spinel castable is mainly made of corundum, super bauxite clinker, fused or high-purity magnesia, and alumina-magnesia spinel, etc., and is configured with low cement technology. This material is also called corundum or high alumina magnesia spinel refractory castable, also called composite alumina magnesia spinel refractory castable. Because it is mostly used in the various ladles, it can also be called ladle castable.
The characteristics of alumina-magnesia spinel refractory castables are high-temperature resistance, strong structural spalling resistance, resistance to chemical corrosion of steel slag, resistance to rapid cold, and rapid heat, non-sticking to molten steel, and resistance to erosion. Use the pouring vibration method for construction.
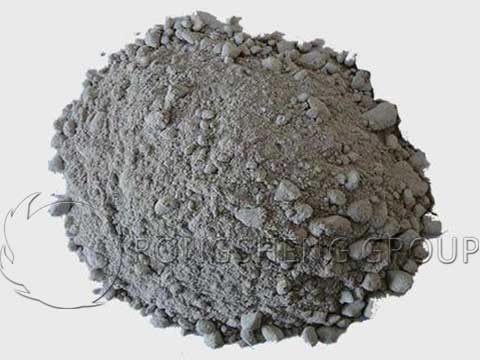
The Bonding Method for Alumina Magnesia Refractory Castables
Binder is an important part of alumina magnesia castables. The bonding methods used for alumina-magnesia castables are generally calcium aluminate cement bonding, silica micro powder bonding, hydrated alumina bonding, sol bonding, magnesium silicon wafer bonding, etc.
Firstly, Cement bonding.
In the early stage of the development of alumina-magnesia castables, pure calcium aluminate cement is used. This is because the cement-calcium aluminate will react with Al2O3 in the matrix to form CA6, which is a highly refractory phase. However, as the amount of cement added increases, the fluidity of the castable decreases. At the same time, due to the excessive content of CaO at high temperatures, it will react with SiO2, Al2O3, and MgO in the matrix to form a low melting phase, which will reduce the high-temperature performance of the castable. Refractory researchers studied the effect of the amount of water added in cement on the thermal expansion behavior of alumina-magnesia castables after high-temperature firing. The results show that as the amount of cement increases, the phases of CA2 and CA6 in the sample increase, and the linear change rate of the sample increases after high-temperature heat treatment. At the same time, some refractory researchers have studied the influence of silica powder, magnesia, and cement on the properties of high-purity alumina-magnesia castables. The study pointed out that the pure calcium aluminate cement and the Al2O3 fine powder in the matrix start to react at about 1000°C to form CA2 and CA6. The reaction is accompanied by volume expansion, which can reduce the strength ratio after high- and medium-temperature firing, and also contribute to the improvement of the high-temperature performance of the sample.
Then, MgO-SiO2-H2O combination.
There are much researches on MgO-SiO2-H2O combination cohesion. The combination of MgO-SiO2-H2O is used in the alumina-magnesia castable. On the one hand, due to the polymerization of SiO2 gel formed by the interaction of SiO2 powder and water, the amount of water added is reduced, and the fluidity of the castable is greatly improved. On the other hand, the combination of MgO-SiO2-H2O can inhibit the hydration of magnesia. However, too much silica powder will form a low melting point phase with impurities in the matrix. At the same time, the forsterite phase formed by the reaction of magnesia and silica powder in the matrix has poor thermal shock stability at high temperatures.
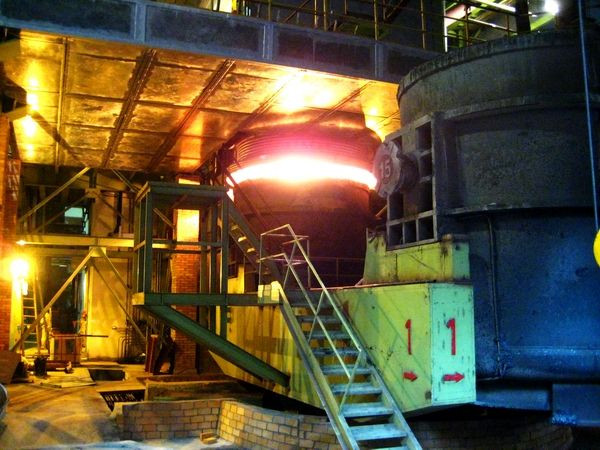
Application of Alumina Magnesia Refractory Castable
Alumina Magnesia Refractory Castables have been widely used in a ladle for medium and small die casting. The average ladle age is 60 to 80 times, and the consumption of refractory materials per ton of steel is reduced by about 70% compared with that of clay ladle bricks. The raw materials of Alumina Magnesia Refractory Castables for ladle are basically the same as alumina-magnesia refractory ramming materials. In order to obtain strength at room temperature, sodium fluorosilicate should be added as a coagulant. The load softening temperature of the ladle alumina-magnesia castable is relatively low, which is the result of the formation of some low-baked substances by adding magnesia powder and the combined effect of water glass and sodium fluorosilicate.

Rongsheng Refractory Castable Manufacturer
Rongsheng is a refractory manufacturer and seller with rich experience. Rongsheng’s refractory castable production line is equipped with advanced fully automatic equipment. The annual output of 80,000 tons of monolithic refractories products. And has rich experience in the configuration and production of ladle refractories. It aims to provide customers with high-quality materials for refractory linings to save production and maintenance costs. If you want to know more about Rongsheng refractory manufacturers, also the alumina bricks manufacturers, get the price of alumina magnesia refractory castables for ladle for free. Please contact us. We are always ready.