Difference Between High Alumina Bricks and Fire Clay Bricks
When buying refractory bricks, some customers may consider whether to buy high alumina bricks or fire clay bricks. This is based on the customer’s actual thermal furnaces’ working conditions, taking the difference between high alumina refractory bricks and fire clay bricks as a reference. High alumina bricks are close to alkaline, and clay fire bricks are close to acid, which is the most essential difference between them.
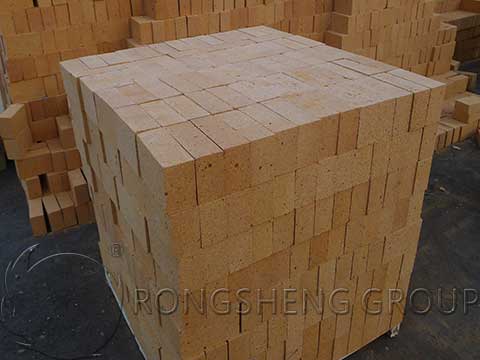
High Alumina Bricks
High alumina refractory brick is an aluminum silicate refractory with an alumina content of more than 48%. It is formed and calcined by alumina or other raw materials with high alumina content. The high alumina bricks have high thermal stability, and the refractoriness is above 1770 ℃. Slag resistance is better. It is mainly used for lining blast furnace, hot blast stove, electric furnace top, reverberatory furnace, and rotary kiln, etc. In addition, high alumina bricks are also widely used as open-hearth regenerative checker bricks, plugs for pouring systems, nozzle bricks, etc.
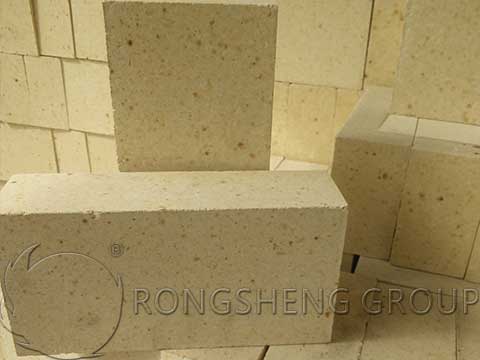
Fire Clay Bricks
The Al2O3 content of the fire clay bricks is 30% ~ 40%. Fire clay bricks are kind of weak acid refractory brick products, which can resist the erosion of acid slag and acid gas. They have weaker resistance to alkaline substances. Clay fire bricks have good thermal properties and are resistant to rapid cooling and heat.
Clay fire bricks are mainly divided into clay fire bricks for blast furnaces, clay refractory bricks for hot blast stoves, and large clay fire bricks for glass kilns according to their uses.
Due to the low load softening temperature of fire clay bricks, shrinkage occurs at high temperatures, the thermal conductivity is 15% to 20% lower than that of silica bricks, and the mechanical strength is also worse than that of silica bricks. Therefore, clay bricks can only be used for secondary parts of coke ovens, such as regenerator wall sealing, small flue lining bricks and regenerator bricks, furnace door lining bricks, furnace roof, and riser lining bricks.
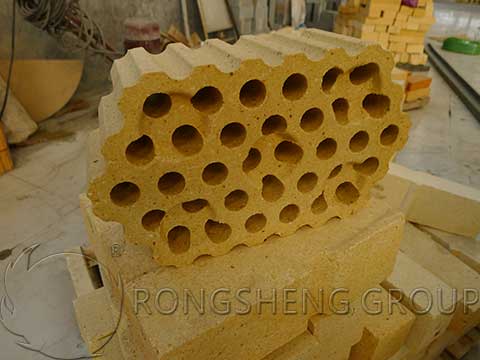
Advantages of Fire Clay Bricks
- Fire clay bricks are weak acid refractory materials and have a certain degree of corrosion resistance to acid slag. Its application is widely, and it is also the refractory material with the largest production volume.
- The price is cheap. Because it mainly uses refractory clay as the raw material, the production cost will be much lower than the refractory bricks using other raw materials.
- Low refractoriness. It can be used in the high-temperature kiln places where do not belong to the high-temperature zone, or other parts that are not important.
Clay Fire Bricks Performance
The fire resistance of clay bricks is comparable to that of silica bricks which can up to 1690 ~ 1730 ℃. But the softening temperature under load is 200 ℃, lower than that of silica bricks. Because the clay brick contains mullite crystals with high refractoriness, it also contains nearly half of the low-melting amorphous glass phase.
In the temperature range of 0 ~ 1000 ℃, the volume expands of clay fire bricks uniformly with increasing temperature. Its linear expansion curve approximates a straight line. The linear expansion rate is 0.6% to 0.7%, only about half of the silicon brick. When the temperature reaches 1200 ℃, and then continue to heat, its volume will begin to shrink from the maximum expansion. The residual shrinkage of clay bricks leads to the cracking of the masonry gray joints, which is a major disadvantage of clay bricks. When the temperature exceeds 1200 °C, the low melting point in the clay brick gradually melts. Due to the surface tension, the particles are very close to each other, resulting in volume shrinkage.
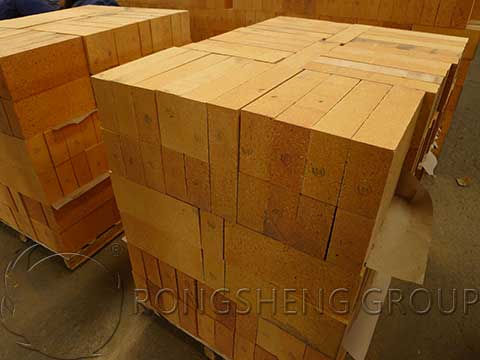
Conclusion
In general, the chemical pH value of high alumina bricks belongs to neutral refractory bricks. Fire clay bricks are neutral refractory bricks that tend to be acidic. High-alumina refractory bricks, all physical and chemical properties except thermal shock resistance, are superior to clay fire bricks. In the construction of kilns lining and other thermal equipment, if the clay refractory bricks are capable of the working environment, it is not necessary to use high alumina bricks.
Of course, due to the limitations of the working conditions of industrial kilns, under certain conditions, certain types of clay bricks or certain types of high-alumina bricks must be used. Under such conditions, to meet the production conditions of industrial kilns as the standard, we will provide customers with high-quality clay bricks and high-alumina bricks. From this point of view, the performance of some clay bricks will be better than that of high alumina bricks.
Want to get the prices of fire clay bricks, and lightweight fire clay bricks, please contact Rongsheng Refractory Bricks Manufacturer. Rongsheng has just delivered 750t low creep low porosity fire clay bricks to customers.