What are the Reasons Why Refractory Bricks Can Resist High Temperatures?
Refractory bricks are inorganic non-metallic materials with a refractory degree of not less than 1580°C. It is a basic material for high-temperature technology, a structural material for masonry kilns and other equipment, and a functional material for manufacturing certain high-temperature containers and components or their special functions. The successful use of refractory bricks under high temperatures must have a good organizational structure, thermal properties, mechanical properties, and usability. That is to say, it has high refractoriness, load softening temperature, thermal shock resistance, and chemical erosion resistance so that it can withstand various powerful chemical changes and other effects, and meet the use requirements of thermal equipment and components. So, why can refractory bricks withstand high temperatures? RS Refractory Materials Manufacturer, a powerful refractory brick manufacturer, ensures that the refractory bricks can withstand high temperatures based on the raw materials of the refractory bricks and the characteristics of the molding and sintering process of the refractory bricks as inorganic non-metallic materials.
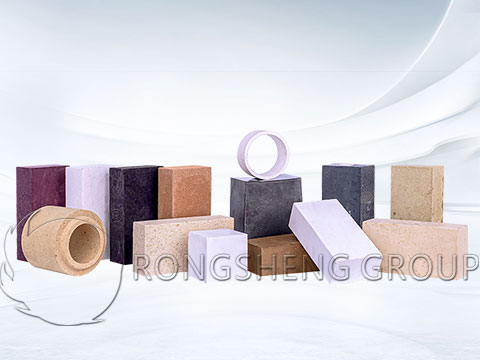
- Raw materials for refractory bricks
The raw materials used in the production of refractory bricks are generally natural ores. Refractory bricks with different properties are made by processing raw materials such as bauxite, silica, and magnesite. Such as aluminum-silicon refractory bricks, siliceous refractory bricks, and magnesia refractory bricks.
Aluminum-silicon refractory bricks are produced using bauxite as raw material. Its main component is alumina. Hydrated alumina containing impurities is an earthy mineral that is insoluble in water and soluble in sulfuric acid and sodium hydroxide solutions. It is mainly used for smelting aluminum and making refractory materials. Because the refractoriness of high-alumina clinker is as high as 1780°C, it has strong chemical stability and good physical properties. The bauxite is purified at high temperature to produce a corundum main crystal phase with an alumina content greater than 90%, which can produce ultra-high temperature refractory bricks – fused zirconium corundum bricks.
The raw material of silica refractory bricks is silica, and its main component is SiO2. The higher the content, the higher the refractory degree. The most harmful impurities are Al2O3, K2O, Na2O, etc. Silica bricks are made from natural silica as raw material, plus an appropriate amount of mineralizing agent to promote the conversion of quartz in the body into tridymite. It is slowly fired at 1350-1430°C in a reducing atmosphere. It has high-temperature strength and the load softening temperature is 1620℃.
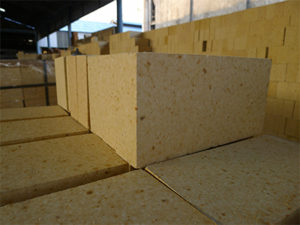
Magnesite is the main raw material for making magnesite refractory bricks. Its basic component is MgO. Magnesium oxide has high refractory insulation properties. It can be transformed into crystals after being burned at high temperatures above 1000°C and becomes sintered magnesia when the temperature rises to 1500-2000°C. Then it can be made into magnesia bricks or magnesia ramming materials after being crushed to a certain particle size or powder. Magnesia refractory bricks are alkaline refractory bricks, which have strong energy resistance to alkaline slag but cannot resist the erosion of acidic slag. The refractoriness is above 2000℃, but its load softening point is only 1500℃, and its thermal shock stability is poor.
- Refractory bricks are inorganic non-metallic materials
Inorganic non-metallic materials, organic polymer materials, and metallic materials are listed as the three major materials. Common inorganic non-metallic materials are characterized by high compressive strength, hardness, high-temperature resistance, and corrosion resistance. In addition, ceramics have excellent corrosion resistance, and refractory materials have excellent properties in heat protection and insulation. These are incomparable to metal materials and polymer materials. However, compared with metal materials, it has low breaking strength and lacks ductility. Compared with polymer materials, they have higher density and complex manufacturing processes.
- Forming and sintering of refractory bricks
The production process of refractory bricks is through mineral crushing-raw material mixing-mechanical molding-high temperature firing. This process finally produces a product that can withstand high temperatures. The sintering temperature of the green body passing through the high-temperature tunnel kiln will be higher than the load-softening temperature of the product. Generally, the sintering temperature is above 1500℃, the refractoriness is above 1770℃, and the high-temperature resistance is good. Refractory bricks are mainly used to build kiln linings such as steelmaking electric furnaces, glass furnaces, and cement rotary furnaces.
To summarize, there are three main reasons why refractory bricks can resist high temperatures. ① The raw minerals used in refractory bricks have high refractoriness. ② As an inorganic non-metallic material, the level of its use is determined by the level of raw materials. ③ The finished body has passed through a high temperature of over 1500°C in a high-temperature tunnel kiln, so the refractory bricks can resist high temperatures and are suitable for use in high-temperature kiln linings.
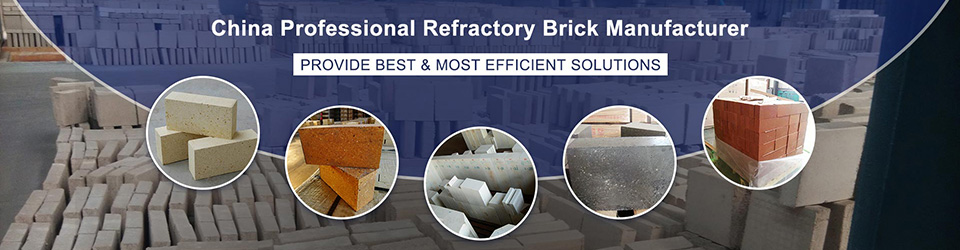
Performance advantages of low porosity refractory bricks
Clay refractory products are extremely versatile and are made of high-quality raw materials. It is an indispensable refractory material for various industrial kilns. Low-porosity clay bricks were originally designed and widely used in hot blast stoves and glass kiln regenerators. Nowadays, it is widely used in lime kilns due to its good density and good resistance to chemical corrosion, especially alkali corrosion.
Low-porosity clay bricks are refractory products made from high-quality burnt gemstones as the main raw material, and their performance has been fully upgraded. The performance advantages of low porosity refractory bricks include.
- Strong corrosion resistance.
- Low porosity and high density.
- High mechanical strength.
- Strong anti-penetration ability.
- High strength and high fire resistance.
- The organization is dense.
- Good thermal shock stability and resistance to peeling.
RS refractory brick manufacturer
RS Refractory Brick Manufacturer is a powerful manufacturer of refractory brick production and sales. Our refractory brick products have an annual output of 60,000 tons, and the quality is reliable and guaranteed. We have also made certain breakthroughs in thermal insulation material products. It has contributed a small step forward for energy-saving and heat preservation of high-temperature industrial furnaces. Our RS company can provide comprehensive refractory services for high-temperature industrial furnaces. Our professional technical team can also provide suitable solutions for the lining of high-temperature industrial furnaces. Material design and construction of refractory linings, and turnkey refractory projects. Contact us to get a free quote and samples.