Non-Burning Bricks for Ladle
Non-burning bricks for ladle include alumina-magnesia bricks, alumina-magnesia-carbon bricks, and magnesia-alumina-carbon bricks. The difference between their fired bricks is that they use water glass or phenolic resin as the bonding agent and undergo low-temperature treatment after molding. During the use of non-fired bricks for ladle, the alumina and magnesia in the matrix form spinel, and the carbon in the graphite and resin binder forms a carbon chain network structure. Therefore, the strength, slag resistance, and thermal shock resistance of refractory bricks for ladle are further improved. To get the price of refractory bricks for ladle for free, please contact Rongsheng refractory brick manufacturer. Next is the introduction of unburned bricks for a ladle.
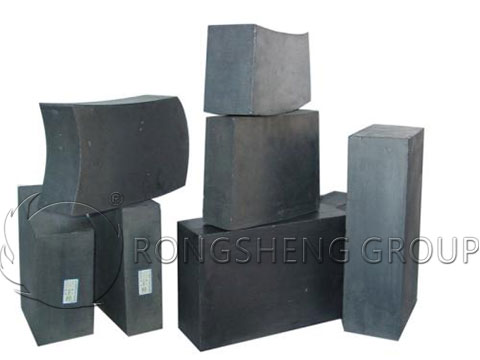
Alumina-Magnesia Brick and Alumina-Magnesia-Carbon Brick
First of all, let’s learn about the non-burning bricks for ladle combined with water glass, including alumina-magnesia brick and alumina-magnesia-carbon brick. The aggregate of the alumina-magnesia brick is generally first-grade bauxite, and the powder is super-grade bauxite clinker powder and first-grade magnesia powder. Use high modulus water glass as the bonding agent. After pressing, the finished product is treated at a low temperature of 150°C. The refractory brick is used on the large and medium-sized die-cast ladle, and its life span is generally 60 to 90 times.
Alumina-magnesia-carbon bricks are successfully manufactured on the basis of alumina-magnesia bricks and magnesia-carbon bricks, and the production process is similar to that of magnesia-carbon bricks. Water glass is combined with alumina-magnesia-carbon bricks, and primary and secondary alumina clinker is used as a refractory aggregate. The first-grade or super-grade high-alumina powder is used as refractory powder, and 8%~13% of the first and second-grade metallurgical magnesia powder is blended. The carbon material adopts electrode powder, earthy graphite, or flake graphite, the amount of which is 3%~8%, and the water glass solution (m=2.4~3.0) is used as the binding agent. After forming, the finished product is processed at a low temperature of 200~250℃. The refractoriness of the water glass bonded alumina-magnesia-carbon brick is 1770℃, and the 4% load softening temperature is 1320~1340℃, which is caused by more Na2O in the binder. If high modulus sodium silicate is used to bring in less Na2O, the load softening temperature will increase to 1410℃, and the refractoriness will be 1790℃. This kind of refractory brick is widely used in medium and small ladle due to its better performance and low price. The refractory brick is applied to the mold-cast ladle, and the slag line area is built with magnesia carbon bricks, and its life span is 50-100 times.
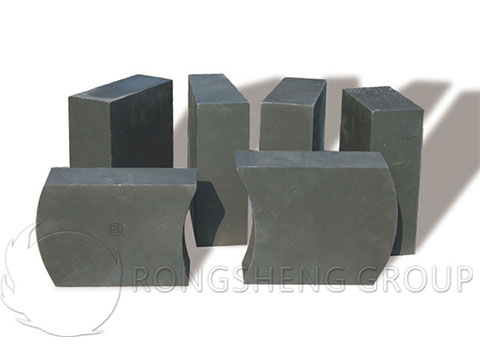
Resin-Bonded Alumina Magnesia Carbon Brick
The raw materials of resin-bonded alumina-magnesia-carbon bricks use first-grade or super-grade bauxite clinker, white corundum, sub white corundum, and magnesia-alumina spinel as aggregates and powders. The magnesia powder is made of high-quality sintered magnesia or fused magnesia with Mg>95%, and mixed with flake graphite, high-quality silicon carbide and alumina powder or SiO2 powder. The phenolic resin binder is used for high-pressure molding, and the bricks are then processed at a low temperature of about 200°C to become the finished product. The refractory brick has the advantages of excellent strength, corrosion resistance, peeling resistance, thermal shock resistance, and non-sticky slag. However, the thermal conductivity is relatively large, and heat insulation measures must be taken during use.
It is better to directly add an alumina-magnesia spinel compound fired material into the alumina-magnesia-carbon bricks than doping with magnesium oxide. Because magnesia oxide can form spinel with alumina during use. Synthetic alumina-magnesia spinel should generally be sintered in a rotary kiln at a temperature greater than 1600°C. The higher the temperature, the better the quality. Its bulk density is 2.95~3.10g/cm3, and its content of alumina and magnesia should be greater than 91%. The fused magnesia-alumina spinel is more expensive. To ensure the quality of refractory bricks, suitable magnesia-alumina spinel should be selected.
Resin-bonded alumina-magnesia-carbon bricks have been widely used in the continuous casting ladle of many steel plants. On the 50-100t steel ladle for continuous casting, mid-grade alumina-magnesia-carbon bricks are used as lining. The slag line area is built with high-quality magnesia carbon bricks, and the service life is generally 50 to 80 times, up to 100 times.
In the 1990s, a large number of high-quality alumina-magnesia-carbon bricks and magnesia-carbon bricks for slag line areas were used in the lining of refining furnaces. The service life of the refining bag is more than 30 times, and the service life of LF(V) of 40~90t is about 50 times.
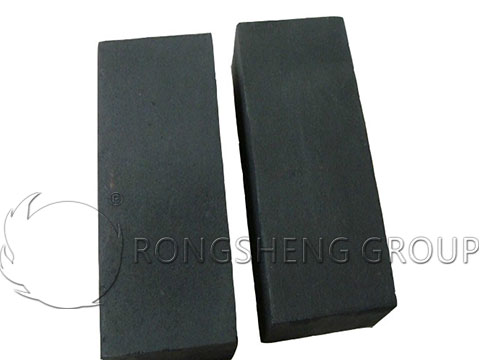
Magnesia Alumina Carbon Brick
The production process of magnesia-alumina-carbon brick and alumina-magnesia-carbon brick is basically the same. It is the pre-synthetic spinel mixed with fused magnesia, and the difference in linear expansion coefficient between the two forms micro-cracks during high temperature and cooling use to buffer the thermal stress generated by temperature changes and reduce thermal spalling. Because the elastic modulus of spinel (MA) and periclase (M) are quite different, the former (0.012~0.022)×106MPa, the latter (0.059~0.49)×106MPa. Tough spinel helps to improve the thermal shock resistance of refractory bricks. In addition, the carbon material is added to the periclase-spinel, and about 10% graphite is added. After making it evenly distributed in the refractory brick body, the carbon atoms form a staggering network structure at high temperature, so that the material has a good high-temperature performance. In addition, graphite has high surface tension and a small wetting angle, which can effectively prevent the penetration of molten slag.
For example magnesia-alumina-carbon bricks for 75t LF lining of a steel plant. MgO 71%, Al2O3 13%, C 10%, apparent porosity 3%, bulk density 3.08g/cm3, compressive strength 50MPa, high temperature flexural strength (1400°C) 8MPa. The slag line uses high-quality MgO-C bricks, with a service life of more than 50 furnaces.
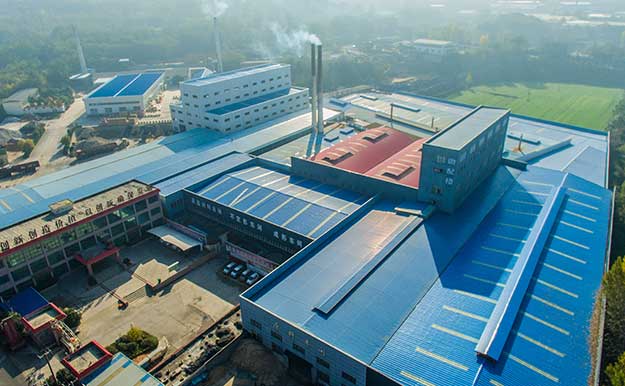
Rongsheng Refractory Brick Manufacturer
Rongsheng is an experienced refractory manufacturer. Rongsheng’s refractory brick products have been recognized by customers in more than 60 countries around the world. Rongsheng’s project of refractory materials for ladle also has very strong competitiveness. If you need to buy refractory materials for ladle, please contact us. We will provide you with services according to your specific needs. You are welcome to consult and learn more about non-burning bricks for ladle.