Development of Refractory Materials for Ladle Lining
The ladle is an extremely important metallurgical equipment in the steelmaking process. Its role is not only the ladle for carrying molten steel in the traditional sense but also the core carrier of the refining process outside the furnace. The choice of Refractory Materials for Ladle Lining is not only related to the life and cost of the ladle but also directly affects the output and cleanliness of molten steel. Let’s look at the use and development of refractory materials for ladle lining in a steel plant in the past 20 years.
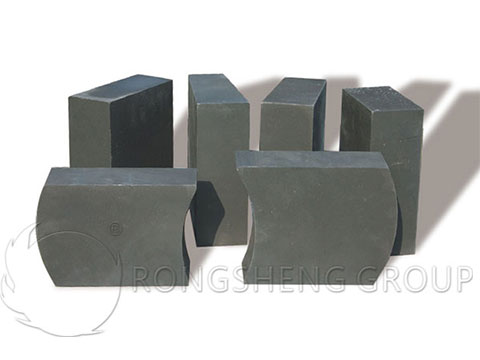
Development of refractory materials for ladle lining
According to a steel mill, they have 3 types of the ladle. In the order of commissioning, they are 120 t ladle, 150 t ladle, and new 150 t ladle, of which the new 150 t ladle is modified from the original 40 t ladle. The refractory materials used in different ladles are different due to different specific production requirements.

40 t ladle
Initially, the lining of the 40t ladle was entirely made of alumina-magnesia machine-made bricks, the thickness of the bottom bricks was 300 mm, and the thickness of the wall was 120 mm. Due to the shortcomings of alumina-magnesia machine-made bricks such as thermal shock stability and poor high-temperature strength, the life of the 40 t ladle bottom is only about 40 furnaces, which cannot be synchronized with the body bricks. Later, magnesia-carbon bricks were used for the bottom of the bag, and alumina-magnesia machine-made bricks were used for the wall and slag line, and the overall service life reached more than 100 furnaces.
120 t ladle
At the initial stage of production, the Refractory Materials for Ladle Lining of 120t ladle is made of alumina-magnesia machine-made bricks, the thickness of the bottom brick is 300 mm, and the thickness of the wall brick is 160 mm. In the early stage, the life of the ladle can be up to 90 furnaces when it is cast directly on the ladle. After the application of the refining process, as the refining ratio continues to increase, the life of the ladle is significantly reduced. The main reason is that the electrodes of the LF refining furnace heat up the molten steel and slag near the slag line, and the alumina-magnesia bricks are quickly melted and lost at high temperatures. In addition, refining will extend the residence time of molten steel in the ladle and also accelerate the erosion of alumina-magnesia bricks. Beginning in 2009, full magnesia carbon bricks have been used in 120t ladle. Magnesia carbon bricks have excellent slag resistance and high-temperature stability, and their service life can reach more than 110 furnaces in a smelting environment with a high refining ratio.
150 t ladle
Steel grades such as cold-rolled plates for automotive plates produced by the 150 t converter system have strict requirements on the carbon content and cleanliness of the molten steel. Therefore, from the initial stage of production, the 150 t ladle has adopted the process route of ladle bottom, clad wall alumina-magnesia machine-made bricks, and slag line magnesia-carbon bricks. At the same time, considering the CAS furnace process, the breathable brick is set in the center of the bottom of the bag, just in the molten steel impact area, and the molten steel has a serious impact on the breathable brick. In addition, due to the poor high-temperature performance of the alumina-magnesia machine-made bricks, the bottom working lining and the air-permeable bricks are severely broken. The life of the ladle is only about 70 furnaces, which cannot meet the needs of production rhythm. Later, magnesia carbon bricks were also used at the bottom of the package, and the problem of broken bricks and excessive melting loss at the bottom of the package was improved.
Application of Carbon-free Lining Materials
After a series of technical optimizations, the steel plant’s refractory materials for ladle are basically finalized. That is, magnesia-carbon bricks with 14% C mass fraction are used for the bottom and slag line, the walls are made of alumina-magnesia machine-made bricks combined with lignosulfonate, and the permanent layer is made of alumina-magnesia castable. The ladle of this material can basically meet the production rhythm of converters and continuous casting at that time. The three bricks and slag line bricks are replaced once every 20-30 furnaces are used, and the slag line bricks are replaced 1 to 2 times during the entire service process. With the development and production adjustment of various steels, the proportion of refining outside the ladle furnace is getting higher and higher. Low-carbon and ultra-low-carbon automobile panels have strict requirements on the carbon content of the lining. Traditional linings can no longer meet the production needs, so carbon-free linings have emerged.
Since 2015, steel plants have tested corundum spinel-based carbon-free materials on 150t ladle and will be promoted throughout the plant in 2016. The upgraded ladle bottom and wall are corundum spinel bricks, and the slag line uses improved magnesia-carbon bricks with 14% C mass fraction.
Corundum Spinel Bricks
The corundum spinel brick is developed under the background of the leapfrog development of refractory raw material production technology. It is a comprehensive upgraded product of alumina-magnesia machine-made bricks. The main raw materials are fused corundum, sintered corundum, fused magnesia fine powder, Al2O3 powder, alumina-magnesia spinel powder, pure calcium aluminate cement, and additives. It has the advantages of good high-temperature stability, strong corrosion-resistance, and high matrix strength.
There are 2 types of corundum spinel brick, organic pressed brick and prefabricated block. The former uses lignosulfonate as the binding agent, and the latter uses cement or alumina gel as the binding agent. The ladle built with prefabricated blocks has a better actual use effect. The machine-made bricks are easy to peel off on the upper part of the bag wall and the bricks are easy to break in the impact area of the bottom of the bag. The main reason is that the machine-made brick fine powder and aggregate are forcibly pressed together by the brick press. During use, the spinel reaction volume expands, which will cause the matrix to crack and become loose. In addition, the critical size of the machine-made brick aggregate is smaller than that of the prefabricated block, and the thermal stress caused by the temperature difference between the hot end and the cold end of the bottom-clad brick can easily break the brick body with a thickness of 300mm. The thermal strength of the prefabricated block is higher than that of the machine-made brick, so the bottom of the prefabricated block is not prone to faults.
The main phases of alumina-magnesia machine-made bricks are corundum, periclase, and mullite. The main phases of corundum spinel machine-made bricks are corundum, periclase, spinel, and α-Al2O3 micro powder. The main phases of the corundum spinel prefabricated block are corundum, spinel, α-Al2O3, and tricalcium aluminate. For details, please see Figure 2.
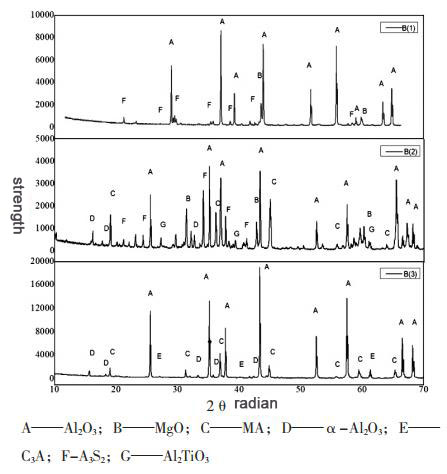
The corundum spinel prefabricated block has two binder systems. One is pure calcium aluminate cement and alumina-rich spinel powder. The other is a gel combination system of ρ-Al2O3 gel, fused magnesia fine powder, and SiO2 fine powder. The prefabricated block of the cement-spinel system has the characteristics of high thermal strength, small volume expansion, and strong erosion resistance, and is suitable for use in the bottom working layer of the package. The prefabricated block of the gel-magnesia fine powder system has good slag resistance and thermal shock performance due to the in-situ generation of magnesia-alumina spinel and is suitable for the working lining of the clad molten pool. Starting in 2018, the steel plant eliminated corundum spinel machine-made bricks. All prefabricated blocks are used for the bottom and wall of the bag, and the melting loss of the working lining is effectively reduced.
High-performance Slag Line Magnesia Carbon Brick
The proportion of LF refining in steel plants is as high as 60%. Some steel grade liquid slags have low basicity, low viscosity, and thin slag layer. These process characteristics bring great challenges to the slag line working layer. The slag line material before 2015 was ordinary magnesia carbon brick, and the main raw materials were ordinary fused magnesia, antioxidant, flake graphite, and phenolic resin. Its corrosion resistance and oxidation resistance are not strong, and the melting rate is very fast. In accordance with the characteristics of the refining process of the steel plant, the magnesia carbon brick formula has been greatly adjusted since 2016. Use 98 fused magnesia as an aggregate and fine powder to improve the corrosion resistance of magnesia carbon bricks. Partially modified graphite is used to replace flake graphite and a nano-carbon source is introduced, which significantly improves the thermal shock resistance and mechanical properties of magnesia carbon bricks. The overall performance of the slag line magnesia carbon brick has been greatly improved.
In recent years, the changes in the physical and chemical properties of ladle slag line bricks are shown in Table 3. Since 2012, the magnesia carbon brick formula has been adjusted three times to improve the grade of magnesia. Improve the performance of graphite, reduce the high-temperature flexural strength to improve corrosion resistance.

Optimization of Permanent Layer Refractory Materials
Before 2016, the permanent layer material used in steel mills’ ladle was traditional alumina-magnesia castable. The mass fraction of alumina is 65% to 70%, and the mass fraction of magnesium oxide is 8% to 10%. The material has the advantages of low cost and good volume stability at medium temperature. However, long-term use in a medium and low-temperature environment has serious attenuation of strength (hereinafter referred to as thermal attenuation), and the problem of poor volume stability at high temperatures is more obvious. In addition, alumina-magnesia castables are heavy materials with high bulk density and large thermal conductivity, which are not conducive to the development of lightweight ladle and the improvement of thermal insulation.
Beginning in 2017, high-alumina castables have been used on the ladle, with a bulk density of 2.453 ~ 2.55g/cm3. It not only guarantees the safety of the permanent layer but also takes into account the heat preservation. Due to the limited crane lifting capacity of the 120t converter smelting system, it is necessary to design a more lightweight ladle permanent layer material. Finally, mullite castable was used, and its bulk density was 2.0~2.1g/cm3. After laboratory tests and field tests, the two new permanent layer materials are significantly better than alumina-magnesia castables in terms of medium and high-temperature strength, volume stability, and corrosion resistance (see Table 4).
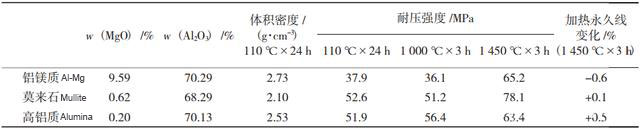
Development Trend of Refractory Materials for Ladle Lining
The general development trend of ladle refractories is to reduce consumption and improve cleanliness. Reducing consumption not only refers to reducing the cost of refractory materials per ton of steel in ladle but also requires reducing the consumption of refractory materials per ton of steel. The purpose is to reduce the pollution of refractory materials to molten steel. To improve cleanliness, on the one hand, use anti-melting lining materials, on the other hand, select non-carbon materials, calcium materials, and other refractory materials that do not pollute molten steel to meet the requirements of producing high-grade clean steel. The next stage of the development direction of steel mill ladle refractories is mainly the following aspects. (1) The permanent layer promotes high-strength and light-weight materials to improve the thermal insulation of the ladle. (2) Promote the whole pouring scheme of the working lining to improve the service life. (3) Establish an information platform for online monitoring of steel ladle, and improve operational safety by implementing safety monitoring.
Learn more about the ladle refractories…