Tundish Refractory
Tundish Refractory Description
The main function of tundish is keeping the temperature of steel liquid stable, making impurity float to the surface of steel liquid, promising the smooth going of the continuous casting during steel liquid shortage or steel ladle changing. The capacity of tundish is usually 15%~30% of steel ladle. Every continuous casting machine will equip 7~12 tundishes. Tundish Steel liquid temperature is 1510~1570℃. Learn more about the tundish refractory, please continue reading.
As a transition device between the ladle and the mold during the continuous casting process, the tundish is not only storage and distributor of the molten steel, but also a refining vessel of the molten steel. It can be used to stabilize the steel flow, reduce the scouring of the billet shell in the mold by the steel flow so that the molten steel has a reasonable flow field and a proper long residence time in the tundish. In order to ensure the uniform temperature of the molten steel and the separation and floating of non-metallic debris, the cleanliness of the molten steel and the continuous casting of multiple furnaces are an important part of improving the quality of steel and the efficiency of continuous casting. The structure diagram of the tundish is shown below.
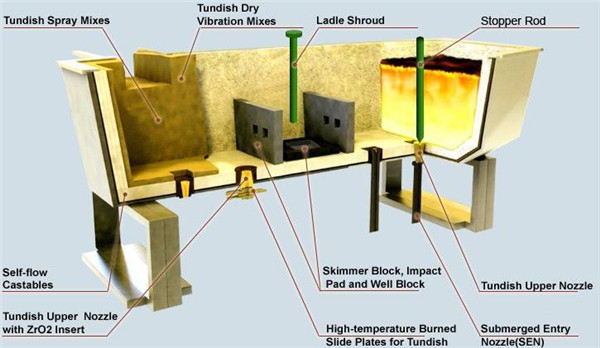
The Main Function of the Tundish
- (1) Diversion of molten steel. For multi-stream and continuous casting machines, the molten steel is distributed to each mold through the tundish.
- (2) Steady flow. Reduce the static pressure of the molten steel to maintain a stable liquid level in the tundish. Pour molten steel into the mold steadily.
- (3) Store molten steel. When replacing the ladle with multiple furnace continuous casting, the drawing speed is not reduced. Create conditions for multiple furnace continuous pouring.
- (4) Purify molten steel. In a long pouring time, the temperature of the molten steel is basically unchanged, and the inclusions in the molten steel are further raised. Avoid contact between molten steel and air, and avoid oxygen and nitrogen absorption.
Refractory Materials for Tundish
Refractory materials for tundish can be divided into three categories in terms of function.
- The first category is lining materials. It is mainly composed of the thermal insulation layer, permanent layer, and working layer.
- The second category is steady flow components. Including slag weir, slag baffle, impact plate, etc.
- The third category is the flow control part. There are stoppers, sliding nozzles, sizing nozzles, and intrusive nozzles.
For billet continuous casting, the core of efficient continuous casting is high drawing speed. This requires that on the basis of the quality of the molten steel meeting the requirements, the continuous operating rate of the continuous caster and the casting speed should be increased as much as possible. To achieve higher billet temperature and cast billet quality. These technical indicators put forward two requirements for tundish refractories, one is a high performance, and the other is long life.
The Flow Control Part of the Tundish
Composition of the Refractory Lining in the Tundish
The tundish is lined with refractory materials and generally includes the following parts. Refractory materials for different parts of the tundish are introduced respectively.
(1) Insulation layer (10-30mm), this layer is next to the steel shell of the tundish. Asbestos boards, insulation bricks, or lightweight castables are usually used. The best effect is aluminum silicate fiber felt, which has low thermal conductivity and is easy to build. Insulating lining. Insulating lining usually adopts clay bricks or insulating board, some steel mills may have no insulating lining.
(2) Permanent layer (100-200mm), which is in contact with the insulation layer. The material is generally clay bricks. The overall permanent lining is the most common, and the castable is generally high-alumina or mullite self-flowing castable. Permanent lining. The permanent lining is made from low cement or ultra-low cement alumina castable, which contains 60%~80% of Al2O3. The service life of permanent lining is between 200~1000 times, or even more.
(3) Working layer (20-50mm), this layer is in contact with molten steel and is the key part. Nowadays, insulation boards or coatings are commonly used. Insulation panels are generally siliceous, magnesia, or forsterite. The paint is magnesia, magnesia chromium, and magnesia calcium. The paint is sprayed mechanically or applied by hand. Corrosion lining. Corrosion lining is made from magnesia coating mix, insulating boards, or dry ramming mass.
(4) The Well Blocks are inlaid at the bottom of the tundish and used to install the tundish nozzle. The material is usually high alumina.
(5) The material of the bottom of the tundish is basically the same as that of the working layer. The bottom working layer of the tundish is easily damaged by the impact of molten steel, which requires corrosion resistance and wear-resistance. High-alumina bricks or dense high-alumina bricks and alumina-chrome bricks are generally used, and large, high-strength tar magnesia bricks are also used. The impact part of molten steel is reinforced with zircon bricks or prefabricated blocks.
(6) The tundish cover covers the tundish, which can play the role of heat preservation and molten steel splashing. The material is made of clay or high-alumina castable as the cover, usually adopts the alumina-silica castable with 60% of Al2O3.
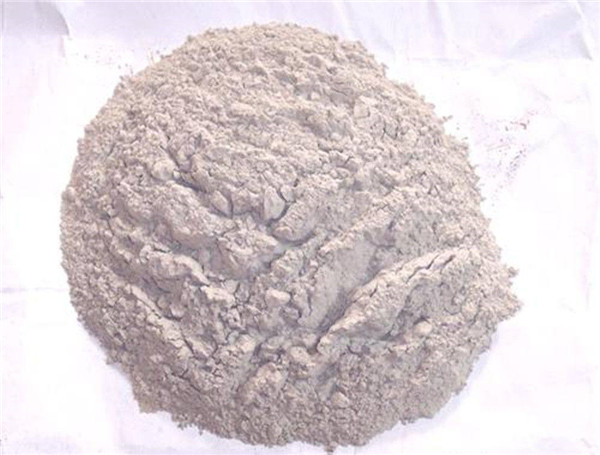
(7) The slag retaining wall (weir), which is built in the tundish, can be a single wall or a double wall. The material of the slag retaining wall weir is usually high-alumina bricks, but can also be made into prefabricated blocks, and its purpose is to block. In order to improve the cleanliness of molten steel, a molten steel filter can also be installed on the slag retaining wall.
- Impaction zone. Impaction zone can use high alumina precast blocks or high alumina bricks, magnesia precast blocks or magnesia carbon bricks can also be used.
- Slag baffle. Slag baffles are mainly made from magnesia precast blocks. Magnesia calcium slag baffle which can adhere impurity in steel liquid is also under development.
- Stopper. Alumina carbon integral stopper.
- Metering nozzle. Zirconia metering nozzle. For small billet continuous casting, metering nozzle zirconia content can reach 94%, bulk density can reach 5g/cm3. Its service life can be longer than 20 hours.
- Upper nozzle. Alumina carbon upper nozzle or sintering mullite upper nozzle.
- Sliding gate. Alumina carbon sliding gate or alumina-zirconia carbon sliding gate.
- Coating mix. Magnesia calcium coating mix can significantly decrease oxygen content and sulfur content in steel liquid, impurity index can decrease 37%.
- Tundish nozzle. Corundum mullite nozzle or alumina carbon nozzle are usually used in the tundish. To avoid blockage during killed steel casting, there is also argon-blowing purging nozzle.
Tundish Refractory Materials Physiochemical Index
Item | LZ-1 | LZ-2 | LZ-3 | LZ-4 | LZ-5 | LZ-6 |
Name | Magnesia chrome coating mix | Magnesia coating mix | Magnesia coating mix | Magnesia coating mix | Magnesia coating mix | Magnesia calcium coating mix |
Cr2O3 % | 5~10 | / | / | / | / | / |
MgO %≥ | 70 | 85 | 85 | 85 | 85 | 70 |
CaO% | / | / | / | / | / | ≥10 |
SiO2 %≤ | 4 | 6 | 6 | 6 | 6 | 6 |
Bulk density g/cm3(110℃,24h) | ≥2.2 | ≥2.2 | 1.8~2.0 | 1.4~1.6 | 1.1~1.25 | ≥1.80 |
Crushing strength Mpa (110℃,24h) ≥ | 4 | 5 | 4 | 3 | 3 | 3 |
Thermal conductivity W·(m·K)-1 (500 ℃) ≤ | 1.2 | 1.0 | 0.8 | 0.6 | 0.4 | 0.8 |
Reheating linear change rate(1500℃,3h) | 0~-1.5 | 0~-2.0 | 0~-2.5 | 0~-2.5 | 0~-2.5 | 0~-3.5 |
Item | LZ-7 | LZ-8 | LZ-9 | LZ-10 | LZ-11 | LZ-12 |
Name | Magnesia dry mix | Magnesia calcia dry mix | Silica insulating board | Silica insulating board | Magnesia insulating board | Magnesia insulating board |
MgO % | ≥90 | CaO 93 | / | / | ≥85 | ≥94 |
CaO% | / | ≥10 | / | / | / | / |
SiO2 % | ≤2 | ≤2 | ≥94 | ≥94 | ≤6 | ≤3 |
Bulk densityg/cm3(110℃,24h) | ≥2.45 | ≥2.4 | ≤1.4 | ≤1.6 | ≤1.5 | ≥2.6 |
Crushing strength Mpa | ≥15 (1500℃,3h) | ≥15 (1500℃,3h) | / | / | ≥20 | ≥30 |
Thermal conductivity W·(m·K)-1 (500 ℃) ≤ | 1.5 | 1.3 | 0.45 | 0.6 | 0.6 | 1.8 |
Reheating linear change rate(1500℃,3h) | 0~-1.0 | 0~-1.0 | 0~2 | 0~2 | 0~-1.5 | ±0.6 |
Item | LZ-13 | LZ-14 | LZ-15 | LZ-16 | LZ-17 | LZ-18 |
Name | High alumina brick | High alumina castable | High alumina castable | High alumina castable | Mullite purging upper nozzle | Alumina carbon down nozzle |
MgO % | 75 | ≥60 | 61.9 | 62.1 | 81.25 | 80.85 |
CaO% | / | ≥10 | / | / | / | / |
SiO2 % | ≤2 | ≤0.7 | 0.64 | 0.68 | / | / |
Apparent porosity % | 19-21 | / | / | / | 21 | 5.5 |
Bulk density g/cm3 | ≥2.5 | ≥2.55 (110℃,24h) | ≥2.39 (110℃,24h) | 2.41 (110℃,24h) | 2.67 | 2.87 |
Crushing strength Mpa | ≥60 | ≥20 (110℃,24h) | ≥14.7 (110℃,24h) | ≥17.6 (110℃,24h) | 83.6 | 101 |
Refractoriness ℃ | >1790 | >1790 | >1790 | >1790 | / | / |
Reheating linear change rate(1500℃,3h) | -0.2~0 | ±0.5 |
Item | LZ-19 | LZ-20 | LZ-21 | LZ-22 | LZ-23 |
Name | Magnesia slag baffle | Magnesia carbon temperature measuring casing | Electric conduction brick | Clay brick | High alumina mortar |
Al2O3 % | / | / | / | >40 | 82.36 |
MgO % | >90 | >70 | >80 | / | / |
(F.C) % | / | >15 | >10 | / | / |
Apparent porosity % | <17 | <5 | <5 | <18 | / |
Bulk density g/cm3 | >2.80 | >2.80 | >2.80 | 2.2 | / |
Crushing strength Mpa | 60 | >20 | >40 | >40 | Adhesion time: 1~3 Min |
Modulus of rupture Mpa | >8 | >10 | >10 | / | 8(1500℃,2h) |