Effects of Kyanite-Mullite on the Properties of Ceramic Burner Bricks
Mullite-andalusite-cordierite bricks have excellent thermal shock resistance and are widely used in hot blast furnace ceramic burners. This paper conducts comparative tests on kyanite-mullite-andalusite bricks and mullite-andalusite-cordierite bricks to analyze the effect of kyanite-mullite on the performance of ceramic burner bricks.
Kyanite-Mullite on the Properties of Ceramic Burner Bricks
Kyanite-mullite is an artificially synthesized mullite raw material made of kyanite as raw material. The kyanite concentrate is crushed, wet-milled, filtered, squeezed into mud, and calcined at 1550℃-1600℃. The physical and chemical properties of kyanite-mullite are shown in Table 1, and the X-ray diffraction analysis spectrum is shown in Figure 1.
Table 1 Physical and chemical properties of kyanite-mullite
Items | Kyanite-Mullite |
Al2O3 % | 46.43 |
SiO2 % | 50.16 |
Fe2O3 % | 0.64 |
TiO2 % | 1.20 |
CaO % | 0.22 |
MgO % | 0.16 |
K2O % | 0.72 |
Na2O % | 0.1 |
Bulk Density g/cm3 | 2.29 |
Apparent Porosity % | 1.3 |
Mullite Phase % | 60 |
Glass Phase % | 30-40 |
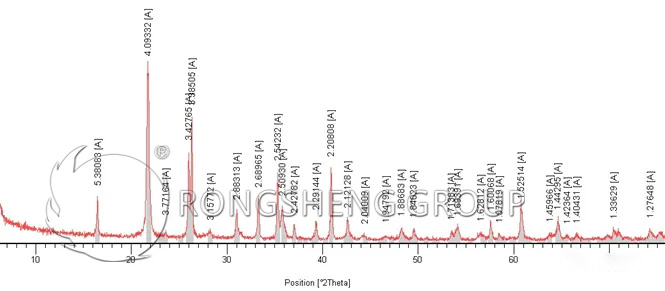
From Table 1 and Figure 1, it can be seen that kyanite-mullite is composed of 60% mullite phase, 30-40% glass phase and 3-5% quartz phase.
This experiment designed two sets of process ratios. Process No. 1 uses alumina-based mullite, garnet and cordierite as the main raw materials. Process No. 2 uses kyanite-based mullite and garnet as the main raw materials. A 50kg mixer was used for mixing, a 400 t press was used for molding, and a tunnel kiln was used for sintering. The test sample is shown in Figure 2, and the results of the physical and chemical properties test are shown in Table 2.
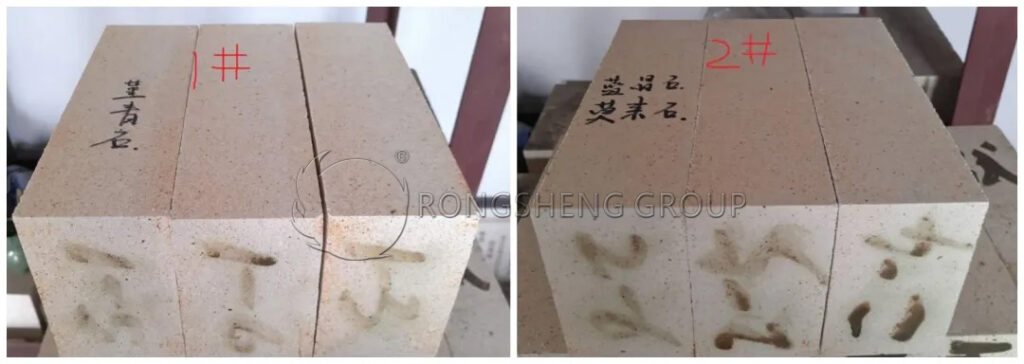
Table 2 Physical and chemical properties test results
Items | 1# | 2# |
Al2O3 % | 61.73 | 61.22 |
Fe2O3 % | 1.00 | 0.96 |
Apparent Porosity % | 22.8 | 19.7 |
Bulk Density g/cm3 | 2.32 | 2.42 |
Compressive Strength MPa | 51.9 | 81.5 |
Load Softening Temperature ℃ T0.6/0.2MPa | 1482 | 1548℃ |
Creep Rate % 0.2MPa | 1250℃x50h -0.622 | 1350℃x50h -0.457 |
Reburning Line Change Rate % 1400℃×2h | +0.1、+0.1 +0.2 | +0.1、+0.2 +0.1 |
Thermal Shock Resistance 1100℃, Water Cooling | >100 | >100 |
It can be seen from Table 2 that the chemical compositions of processes No. 1 and No. 2 are similar. The porosity, bulk density, compressive strength and load softening temperature of process No. 2 are significantly better than those of process No. 1. The load softening temperature of process No. 2 is 68°C higher than that of sample No. 1. This is because after the temperature reaches 1460°C, cordierite is completely decomposed into mullite and glass phase. The raw materials of synthetic cordierite used in refractory materials have a high impurity content (in order to expand the temperature range of cordierite formation and promote sintering), so the high-temperature performance is general. Kyanite-based mullite has a low impurity content, a high main crystal phase content, and a good crystal shape. The high-temperature performance (including load softening temperature and creep rate) is much higher than other aluminum-silicon raw materials with the same aluminum content.
The number of thermal shock resistance (1100°C water cooling) of processes No. 1 and No. 2 is greater than 100 times, which meets the requirement of thermal shock performance of ceramic burner bricks > 100 times. The test bricks after 100 thermal shocks are shown in Figure 3. As can be seen from Figure 3, although both can complete 100 thermal shock tests without damage, the number, width and length of cracks in process 1 are significantly smaller than those in process 2. This shows that mullite-andalusite-cordierite bricks have better thermal shock resistance.
Analysis shows that kyanite-based mullite is a mullite-high silica glass composite material. Its well-developed mullite crystals, uniformly distributed network structure and high-viscosity silicon-rich glass phase all have an improving effect on the thermal shock resistance of the material. In particular, the presence of its high-viscosity glass phase can not only reduce the slip between crystals at high temperatures and improve the thermal mechanical properties of the material, but also inhibit crack extension.
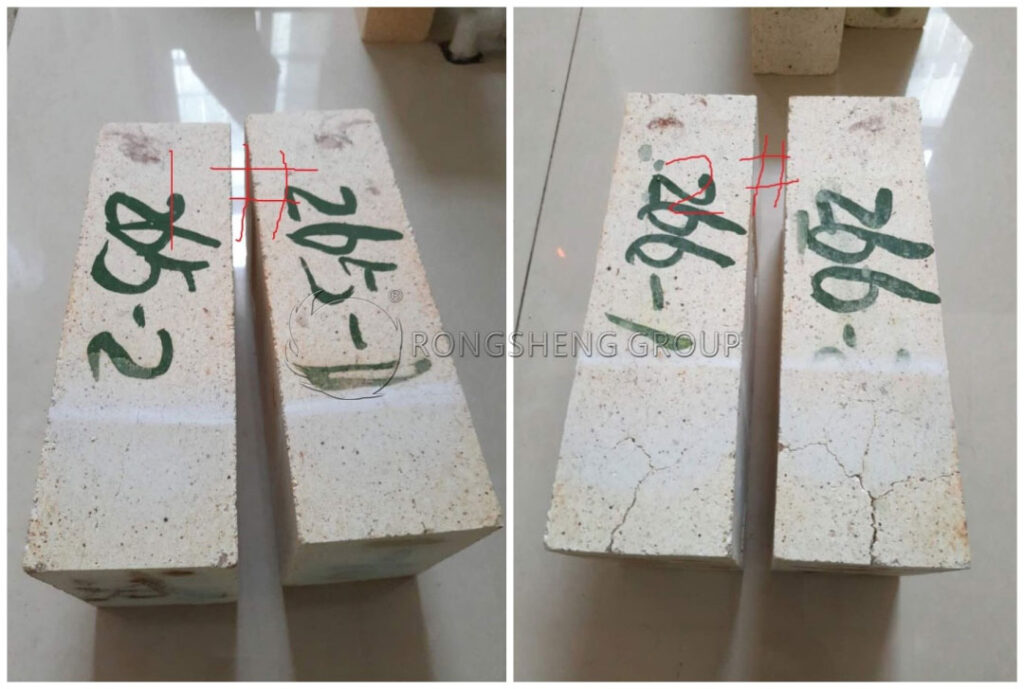
The following conclusions were drawn through test data analysis:
- The apparent porosity, bulk density, load softening temperature and creep rate of kyanite-mullite-andalusite bricks are better than those of mullite-andalusite-cordierite bricks.
- The thermal shock of kyanite-mullite-andalusite bricks is greater than 100 times, which can meet the most demanding thermal shock requirements of hot blast furnace ceramic burners. However, mullite-andalusite-cordierite bricks have better thermal shock resistance.
- Kyanite-mullite-andalusite bricks can replace mullite-andalusite-mullite-cordierite bricks and be used in hot blast furnace ceramic burners.
Semi-Cordierite Bricks and Kiln Furniture
Semi-cordierite bricks are a type of refractory material with cordierite (2MgO·2Al2O3·5SiO2) as the main component. Pure cordierite contains 13.7% magnesium oxide (MgO) and has the following characteristics: Low thermal expansion coefficient of 3×10-6/℃. Due to the low thermal expansion coefficient, cordierite materials generally have excellent thermal shock resistance.
Pure cordierite is an expensive material, so semi-cordierite materials with lower purity are often used as substitutes. Semi-cordierite materials also exhibit a lower thermal expansion coefficient.
Semi-cordierite materials are often used as kiln furniture, kiln car fixing blocks and ceramic parts for ceramic kilns. In some cases, alumina-silicate materials are also used for the same product applications. Table 7 lists the characteristics of some semi-cordierite products used for kiln furniture/kiln blocks. The maximum service temperature of these products is generally 1200℃ or higher.
Table 7 shows the relationship between magnesium oxide content and thermal expansion coefficient. When magnesium oxide content is very low, the thermal expansion coefficient is close to that of clay brick or mullite [about 6×10-6/℃].
Figures 5 and 6 show the microstructure of typical products of this type.
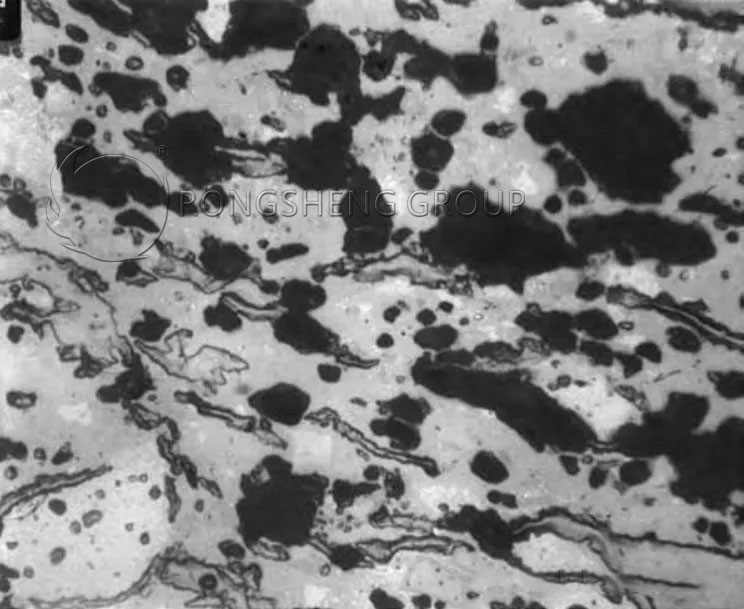
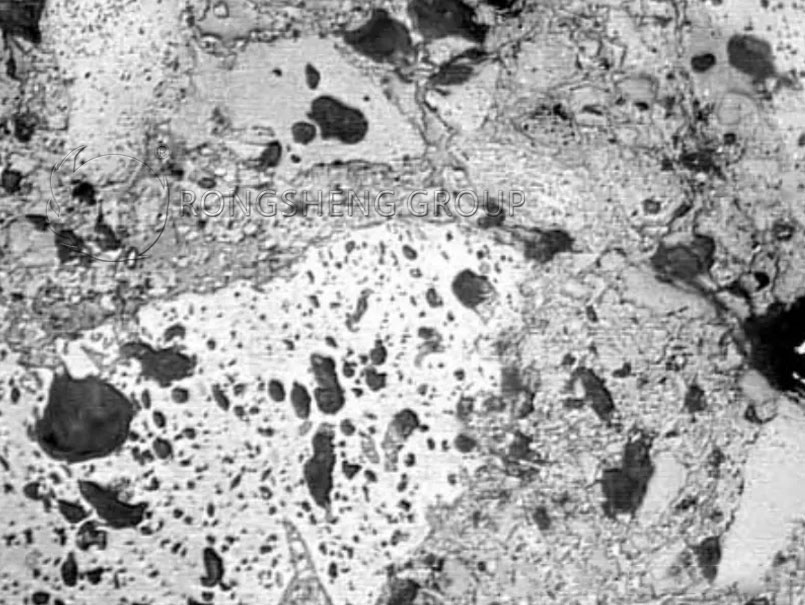
The microstructure of semi-cordierite material shows “crack-shaped” pores, which are typical of extruded clay products (Figure 5). It is not obvious from this micrograph that the size of the pyrophyllite aggregate particles is large, sometimes approaching 3 to 4 mm. In contrast, the microstructure of the pressed semi-cordierite material shows that the refractory aggregate particles are surrounded by a sintered clay matrix and the pores are mainly round (Figure 6). Many authorities believe that the presence of fine round pores improves thermal shock resistance. Therefore, a pressed product with a magnesium oxide content of about 0.9% (Table 7) may have similar properties to an extruded product with a magnesium oxide content of 3.0%.
The typical impurity in semi-cordierite bricks is cristobalite. When the refractory material is fired at a temperature of at least 1300°C, the “free” silicon dioxide (SiO2) or quartz in the raw material is converted to cristobalite. By reference to the MgO-Al2O3-SiO2 phase equilibrium diagram (not shown), it can be seen that free cristobalite is an equilibrium phase unless the composition of the product is exactly the same as pure cordierite. Too high a cristobalite content will cause “caking” and reduce the life of the kiln furniture/kiln blocks. Cristobalite is conveniently determined by X-ray diffraction (XRD) or thermal analysis (TA) techniques.