Alumina Bricks Manufacturing Process
Alumina brick is a high-performance refractory material whose main component is alumina (Al2O3). Usually, high-purity alumina is used as raw material, which is sintered at high temperatures. As a high-quality supplier of alumina refractory bricks, RS Alumina Bricks Factory can provide high-quality Alumina Bricks for high-temperature kiln lining. Contact us for free alumina bricks price.
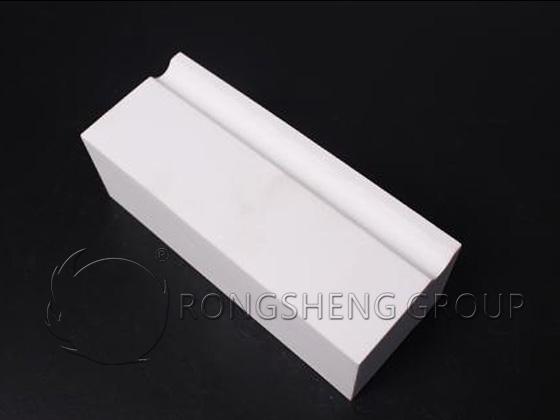
Alumina Bricks Properties
- High-temperature stability. Alumina bricks can work stably for a long time at high temperatures, and their service temperature can reach about 1700°C.
- Corrosion resistance. The main component of alumina bricks is alumina, which is not easily corroded by acids and alkalis.
- High strength and high hardness. Alumina bricks have high hardness, high strength, and good compressive and flexural strength.
- Wear resistance. Wear Resistance Alumina bricks have a smooth surface and are not easily worn, so they have good wear resistance.
Alumina Bricks Use
Alumina bricks have a wide range of application scenarios and are mainly used in various refractory equipment in harsh environments such as high temperature, high pressure, and corrosion. Such as blast furnaces in the metallurgical industry, steel smelting furnaces, aluminum electrolytic cells, etc. High-temperature reaction kettles and high-temperature drying furnaces in the chemical industry. Boilers, kilns, coal-fired gasifiers, etc. in the power industry. As well as cement kilns and glass kilns in the building materials industry. In addition, alumina bricks are widely used in scientific research, aerospace, nuclear industry, and other fields.
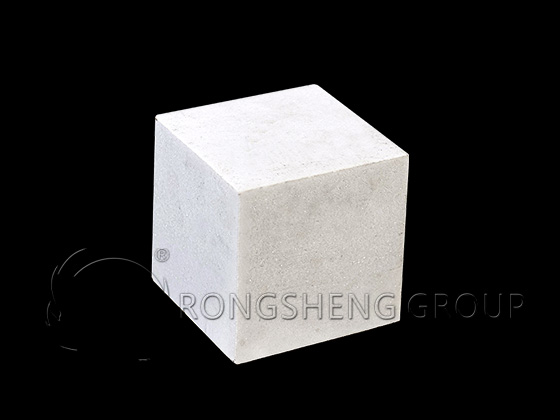
Alumina Bricks Manufacturing Process
After years of accumulation of production and sales experience, RS Alumina Bricks Factory has a further understanding of the production process of alumina refractory bricks.
- Selection of binders
The manufacture of high alumina bricks usually uses soft clay as a binder. The main function of clay in the batching is to improve the formability of the mud and to make the formed and dried green body have a certain strength. The added amount of clay powder in the batching is generally 5%. In order to produce volume-stable low-level high-alumina bricks, high-alumina bauxite powder can be used as a high-alumina binder. Or use high-alumina bauxite powder and clay powder in a predetermined ratio to prepare synthetic mullite as a binder, and a volume-stable high-alumina brick without secondary expansion can be obtained.
- Determination of Particle Composition
The particle composition of high alumina bauxite clinker has an important influence on the forming operation, green body density, high alumina brick density, and strength. Therefore, determining a reasonable particle composition according to different molding methods is an important process factor to stabilize the process operation and improve the quality of high-alumina bricks.
The principle of determining particle gradation is to form a good bulk density, which has no adverse effect on the performance and appearance quality of high alumina bricks. For low-grade bricks, the volume expansion caused by the secondary mullite reaction should also be considered.
High alumina bricks usually use coarse, medium, and fine three-level ingredients. However, secondary or quaternary ingredients may also be used. When using three-level batching, the critical size of each particle size is coarse particle 3-0.5mm, medium particle 0.5-0.1mm, and fine powder <0.1mm.
Production practice shows that when determining the particle size, appropriately increasing the size and quantity of coarse particles can increase the bulk density of the mud, and it is easy to shape. During firing, due to the small specific surface area of large particles, the secondary mullite reaction around the material is weakened, which is beneficial to the sintering of the green body. In turn, the air-packing rate of high-alumina bricks is reduced, the softening temperature under load and compressive strength are improved, and the thermal stability is improved.
There is a limit to the enlargement of the particle size. If the size of the coarse particles increases to 4-5mm, the corners of the high alumina bricks and the uniformity of the structure will be affected, and the larger the clinker particles, the larger the particle segregation during the production process. Therefore, the maximum particle critical size should not be too large. The maximum critical particle size is preferably 3 mm.
The fine powder in the ingredients is beneficial to the sintering of the green body and the increase of the density of the high alumina brick. Adding an appropriate amount of fine powder can not only make the secondary mullite reaction that occurs during the firing of high-alumina bricks proceed in the fine powder. Prevent the green body from loosening due to the secondary mullite ratio reaction around the coarse particles. Moreover, the firing shrinkage caused by the sintering of the fine powder can weaken or offset the volume expansion caused by the secondary mullite reaction. It is advisable to add about 50% fine powder.
The intermediate particles in the ingredients have neither the skeleton effect of coarse particles nor the sintering effect of fine powder. In the production process, according to the specific conditions of production, the addition of intermediate particles is usually limited to a minimum amount. Generally speaking, the additional amount of intermediate particles is about 10%.
In short, to determine a reasonable particle ratio, it is necessary to consider the reasonable bulk density, limit the number of intermediate particles added, and also according to the different molding methods. The performance and requirements of high alumina bricks are used to determine the critical size and the number of particles added at all levels. In the general brick-making process, the upper limit of coarse particles is usually 2-3mm, and the addition amount is 40-45%. For special-shaped high alumina bricks, the upper limit of coarse particles can be reduced to 1-2mm. It is advisable to limit the addition of 1-0.1mm intermediate particles to 10-20%. The amount of fine powder <0.1mm added should be controlled at 40-50%.
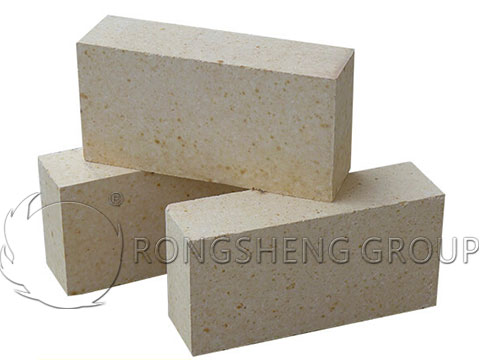
High Alumina Bricks Properties
High alumina bricks for steel manufacturing are made from a special grade of bauxite as the main raw material. Small amounts of white fused alumina and alumina powder are added. Shaped by high pressure, sintered at high temperature. The main mineral composition includes mullite and corundum, which have excellent high-temperature physical properties and chemical resistance. high alumina bricks properties, high alumina bricks have the advantages of small temperature creep, strong corrosion resistance, thermal shock resistance, and stability. It is suitable for large and medium-sized hot air stoves. High alumina bricks are mainly used in masonry blast furnaces, hot blast stoves, electric furnace roofs, blast furnaces, and rotary kiln linings. In addition, high alumina bricks are also widely used as open hearth regeneration inspection bricks, gating systems, nozzle bricks, and other plugs.
RS Alumina Bricks Factory has advanced production equipment and the support of a strong technical team, and strives for excellence in the production of aluminum bricks. It aims to provide high-quality refractory products for customers’ high-temperature kiln linings to save production costs. At the same time, our customer service runs through the entire service life of our refractory bricks in the kiln lining. To choose an aluminum brick manufacturer, you must choose a manufacturer with strength and guaranteed customer service. In addition to our customer service, we also provide the design and construction of refractory lining solutions. Contact us for free quotes and samples.